The Wonders of Electronics Encapsulation Epoxy: Ensuring Durability and Reliability
The Wonders of Electronics Encapsulation Epoxy: Ensuring Durability and Reliability
In the intricate world of electronics, where miniaturization and efficiency reign supreme, durability and reliability are crucial aspects often overlooked. Electronics encapsulation epoxy, a material with remarkable properties, stands as a silent guardian, ensuring the longevity and resilience of electronic devices. This article delves into the depths of electronics encapsulation epoxy, unraveling its significance, applications, and the science behind its effectiveness.
Understanding Electronics Encapsulation Epoxy:
Electronics encapsulation epoxy is a specialized polymer that is a protective coating for electronic components and assemblies. It protects delicate circuits, wires, and elements from environmental factors such as moisture, chemicals, heat, and mechanical stress. This encapsulation process involves covering the electronic assembly with a layer of epoxy resin, which subsequently hardens into a durable and protective shell.
The Science Behind Its Effectiveness:
At the heart of electronics encapsulation epoxy lies its chemical composition, typically consisting of epoxy resin, hardeners, and additives. Epoxy resin, derived from petroleum, is known for its excellent adhesion, mechanical strength, and chemical resistance. When combined with hardeners, a chemical reaction occurs, leading to cross-linking and forming a three-dimensional network; this network structure imparts rigidity and durability to the epoxy, making it an ideal candidate for encapsulation purposes.
Moreover, additives such as fillers, flame retardants, and UV stabilizers can be incorporated into the epoxy formulation to enhance specific properties tailored to the application requirements. For instance, adding fillers like silica can improve thermal conductivity, while flame retardants enhance fire resistance, ensuring safety in high-risk environments.
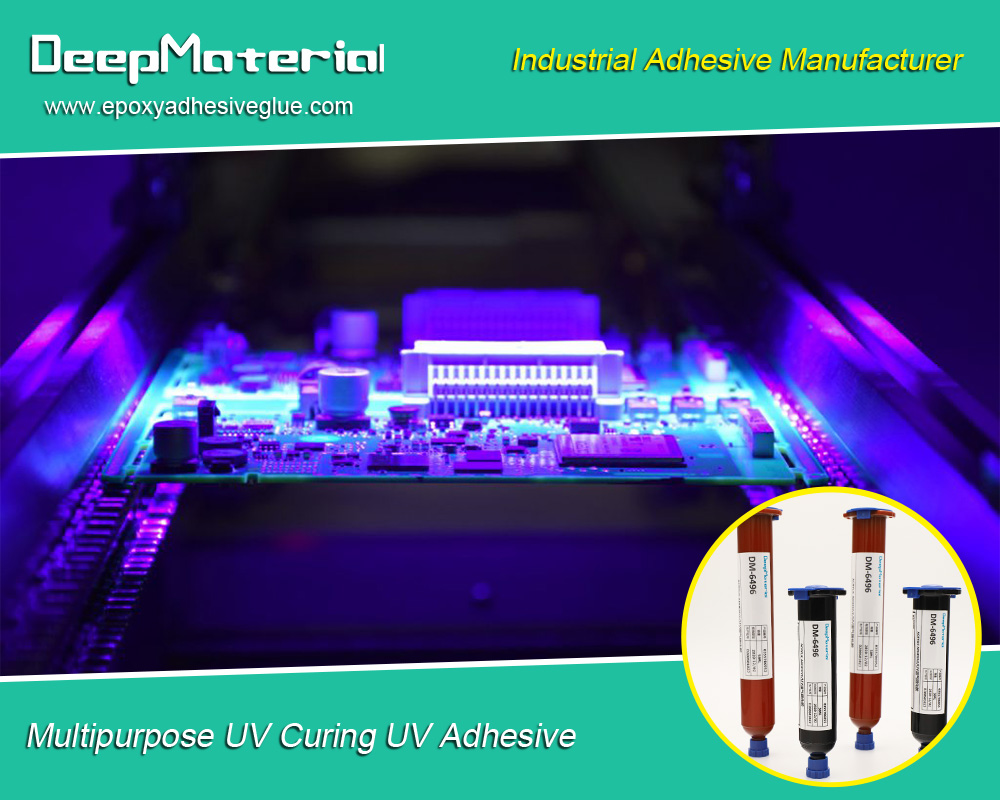
Applications Across Industries:
The versatility of electronics encapsulation epoxy renders it indispensable across various industries, each with its unique challenges and requirements.
- Electronics Manufacturing: In electronics manufacturing, where miniaturization is critical, encapsulation epoxy plays a vital role in protecting sensitive components from moisture, dust, and corrosion. Printed circuit boards (PCBs), sensors, and integrated circuits (ICs) benefit from encapsulation, ensuring reliability even in harsh operating conditions.
- Automotive Electronics: With the automotive industry embracing advanced electronic systems for enhanced performance and safety, the demand for robust encapsulation solutions is rising. Electronics encapsulation epoxy shields control units, sensors, and wiring harnesses from temperature fluctuations, vibration, and chemical exposure, thereby extending the lifespan of critical automotive components.
- Aerospace and Defense: In aerospace and defense applications, where reliability is paramount, electronics encapsulation epoxy withstands extreme temperatures, altitude changes, and mechanical stress. Avionics, communication equipment, and missile guidance systems rely on epoxy encapsulation to maintain functionality in demanding environments.
- Consumer Electronics: From smartphones to wearable devices, consumer electronics are subjected to everyday wear and tear. Encapsulation epoxy protects delicate electronic assemblies from accidental spills, impact damage, and exposure to the elements, ensuring longevity and user satisfaction.
- Renewable Energy: In the renewable energy sector, where solar inverters and wind turbine controllers are exposed to outdoor elements, encapsulation epoxy provides a barrier against moisture ingress, UV radiation, and temperature fluctuations. This enhances the reliability and efficiency of renewable energy systems, contributing to the widespread adoption of clean energy technologies.
Advantages Of Alternative Encapsulation Methods:
While various encapsulation methods exist, electronics encapsulation epoxy offers distinct advantages that set it apart:
- Versatility: Epoxy encapsulation can accommodate complex shapes and configurations, making it suitable for various electronic assemblies.
- Chemical Resistance: Epoxy resins exhibit superior resistance to chemicals, solvents, and corrosive agents, ensuring long-term protection for electronic components.
- Mechanical Strength: The rigid nature of cured epoxy provides mechanical support and vibration damping, reducing the risk of component failure due to stress or impact.
- Thermal Stability: Epoxy encapsulation maintains electrical insulation properties even at elevated temperatures, safeguarding components from thermal degradation.
- Cost-Effectiveness: Despite its advanced properties, epoxy encapsulation remains cost-effective compared to alternative methods such as potting compounds or conformal coatings.
Future Trends and Innovations:
As technology continues to evolve, so do the requirements for electronics encapsulation. Future trends and innovations in this field are poised to address emerging challenges and unlock new possibilities:
- Nanotechnology: Integrating nanomaterials into epoxy formulations holds promise for enhancing properties such as conductivity, thermal dissipation, and mechanical strength, opening doors to next-generation encapsulation solutions.
- Bio-Based Epoxies: With growing environmental consciousness, developing bio-based epoxy resins derived from renewable sources presents an eco-friendly alternative without compromising performance.
- Brilliant Encapsulation: Incorporating intelligent functionalities such as self-healing capabilities or embedded sensors within epoxy encapsulation systems could revolutionize predictive maintenance and extend the lifespan of electronic devices.
- Additive Manufacturing: Advances in additive manufacturing techniques enable the direct printing of encapsulation structures, offering greater design flexibility and customization for specific applications.
Challenges and Considerations:
Despite its numerous benefits, electronics encapsulation epoxy also presents challenges and considerations that engineers and manufacturers must address:
- Curing Time: The curing process of epoxy encapsulation can be time-consuming, impacting production timelines. Optimization of curing parameters and using curing accelerators are essential to mitigate delays.
- Adhesion: Ensuring proper epoxy adhesion to various substrates is crucial for long-term reliability. Surface preparation and compatibility testing are necessary to achieve strong adhesion and prevent delamination.
- Thermal Management: While epoxy provides thermal insulation, it can also trap heat generated by electronic components, leading to thermal stress and reduced performance. Incorporating thermal management solutions such as heat sinks or thermal interface materials is vital for dissipating heat effectively.
- Flexibility vs. Rigidity: The rigidity of cured epoxy may not be suitable for applications requiring flexibility or shock absorption. Selecting the appropriate epoxy formulation with tailored mechanical properties is essential to meet the specific needs of each application.
- Environmental Impact: Traditional epoxy resins derived from petroleum raise concerns regarding environmental sustainability and carbon footprint. Exploring alternative eco-friendly formulations and recycling methods can mitigate the environmental impact of epoxy encapsulation.
Best Practices for Effective Encapsulation:
To maximize the benefits of electronics encapsulation epoxy and ensure optimal performance, adherence to best practices is paramount:
- Design for Encapsulation: Incorporate encapsulation considerations into the design phase of electronic devices to facilitate seamless integration and maximize protection.
- Material Selection: Choose epoxy formulations tailored to the application requirements, considering operating environment, temperature range, and chemical exposure.
- Surface Preparation: Thoroughly clean and prepare substrate surfaces to promote adhesion and minimize the risk of contamination, ensuring a solid bond between epoxy and components.
- Quality Control: Implement rigorous quality control measures throughout the encapsulation process to detect defects, ensure uniform coating thickness, and verify compliance with performance standards.
- Testing and Validation: Conduct comprehensive testing and validation procedures to assess the effectiveness of encapsulation in protecting electronic components against environmental stressors and ensuring long-term reliability.
By adhering to these best practices, manufacturers can harness the full potential of electronics encapsulation epoxy, mitigating risks and maximizing the lifespan of electronic devices.
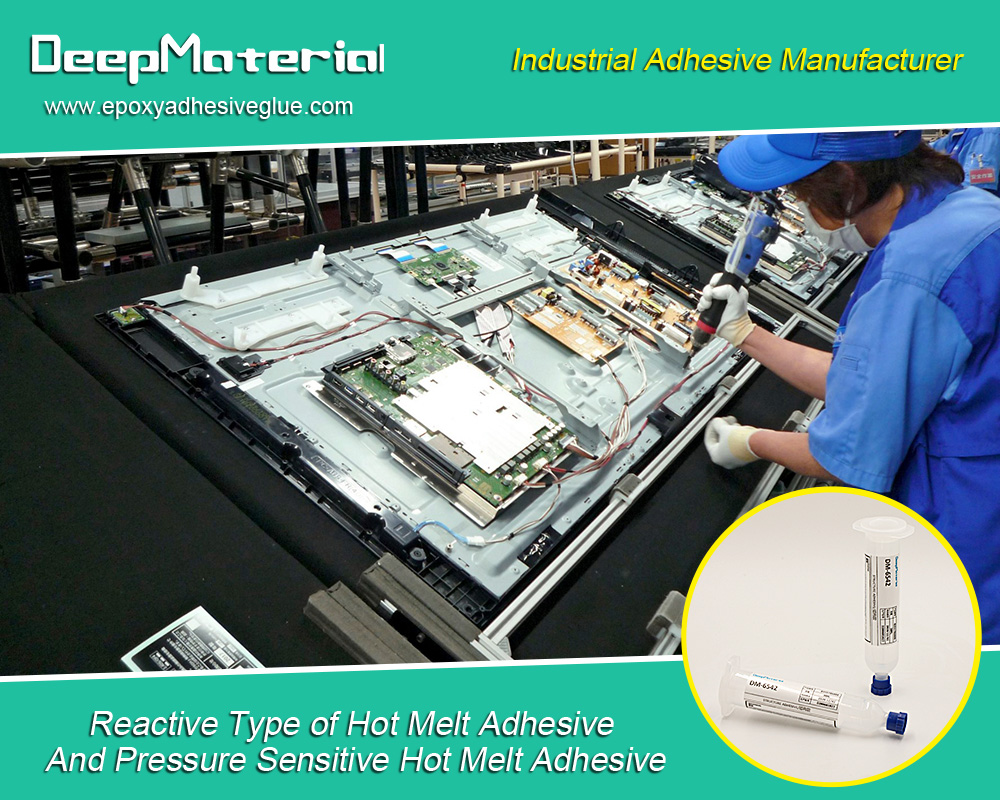
Conclusion:
In the ever-expanding landscape of electronics, where innovation and reliability converge, electronics encapsulation epoxy is a cornerstone of protection and longevity. From the intricate circuitry of consumer gadgets to the critical systems powering aerospace exploration, the role of epoxy encapsulation in safeguarding electronic components is indispensable.
As technology advances and challenges evolve, continuous research and innovation will drive the evolution of encapsulation materials and techniques, pushing the boundaries of durability, reliability, and sustainability. By embracing best practices, addressing challenges, and staying abreast of emerging trends, engineers and manufacturers can confidently navigate the complexities of electronics encapsulation, ensuring the resilience and longevity of electronic devices for generations to come.
For more about choosing the wonders of electronics encapsulation epoxy: ensuring durability and reliability, you can pay a visit to DeepMaterial at https://www.epoxyadhesiveglue.com/category/epoxy-adhesives-glue/ for more info.