Analysis of the Differences in Epoxy Resin Encapsulation Technology between High-Power LEDs and Small-Size LEDs
Analysis of the Differences in Epoxy Resin Encapsulation Technology between High-Power LEDs and Small-Size LEDs
Differences in Optical Performance
Optical Requirements of High-Power LEDs
- High Light Transmittance and Low Light Decay: In order to achieve efficient light output, high-power LEDs have extremely high requirements for the light transmittance of the epoxy resin encapsulation material. Generally, it is required that the light transmittance reaches more than 90% within the visible light range to reduce the absorption and scattering losses of light in the encapsulation material. At the same time, since high-power LEDs generate a large amount of heat during operation, which is likely to cause the aging of the epoxy resin and light decay, it is necessary to select an epoxy resin with good anti-aging performance to ensure that the light decay is small during long-term use and maintain a stable light output.
- Precise Optical Design: In some high-power LED lighting applications, such as street lamps and projectors, precise control and distribution of light are required. Epoxy resin encapsulation can achieve the collimation, focusing, or diffusion of light through special optical designs, such as lens structures and reflective cups, to meet the needs of different lighting scenarios.
Optical Requirements of Small-Size LEDs
- High Color Purity: Small-size LEDs are often used in the display field, such as mobile phone screens and LED displays, and have extremely high requirements for color purity. The epoxy resin encapsulation material should have an extremely low impurity content to avoid interfering with the light color emitted by the LED chip and ensure that the displayed images are vivid and accurate in color.
- Optical Consistency at Small Sizes: Due to the small size of the chips in small-size LEDs, it is difficult to ensure the consistency of the optical performance of each LED during the encapsulation process. The epoxy resin encapsulation process needs to be precisely controlled to ensure that the optical parameters of each small-size LED, such as the emission angle and light intensity, are as consistent as possible, thereby improving the uniformity of the display image.
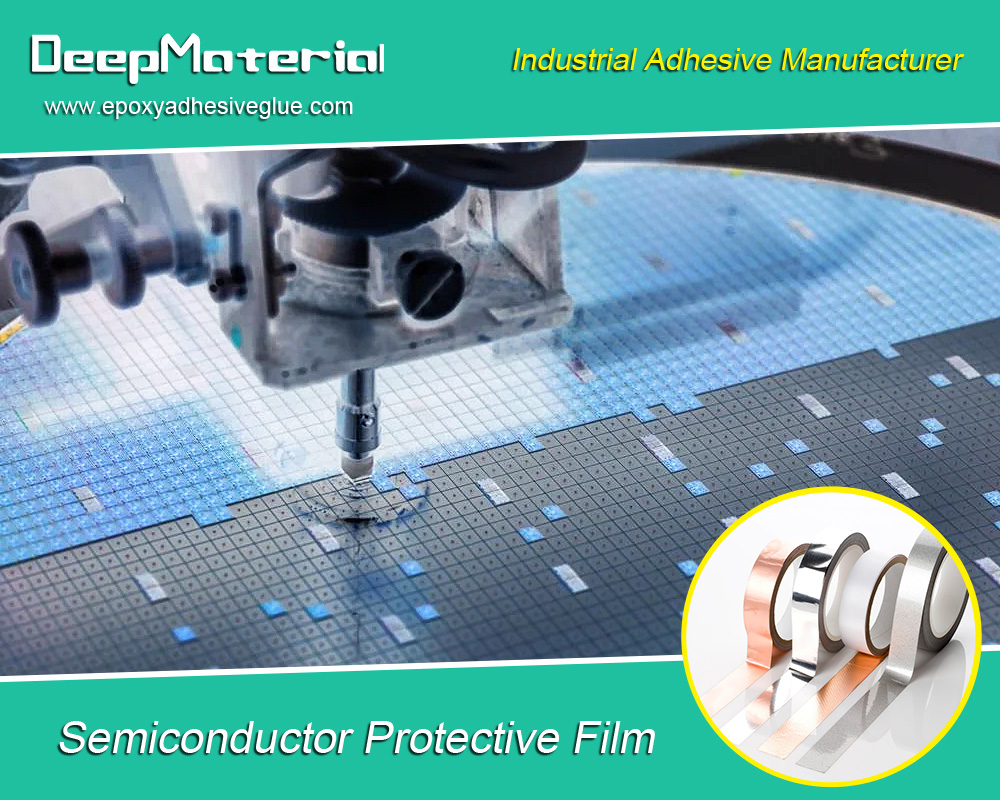
Differences in Thermal Performance
Thermal Performance Requirements of High-Power LEDs
- Good Heat Dissipation: High-power LED chips generate a large amount of heat during operation. If the heat cannot be dissipated effectively in a timely manner, it will cause the temperature of the chip to rise, which in turn affects its luminous efficiency and lifespan. The epoxy resin encapsulation material should have a certain thermal conductivity to quickly conduct the heat generated by the chip. In addition, auxiliary heat dissipation measures such as adding heat sinks and thermal conductive adhesives to the encapsulation structure can also be adopted to improve the overall heat dissipation performance.
- Thermal Stability: High-power LEDs require the epoxy resin encapsulation material to maintain stable performance under different operating environment temperatures. In a high-temperature environment, the epoxy resin should not soften or deform; in a low-temperature environment, it should not crack or have other problems. Therefore, it is necessary to select an epoxy resin material with a relatively wide operating temperature range.
Thermal Performance Characteristics of Small-Size LEDs
- Relatively Lower Heat Dissipation Requirements: Since the power of small-size LEDs is relatively low, the heat generated by them is relatively small, and the requirements for heat dissipation are relatively less stringent. However, with the continuous increase in the integration of small-size LEDs, when multiple chips are densely arranged, a certain amount of heat will still be generated. It is still necessary for the epoxy resin encapsulation material to have a certain thermal conductivity to ensure the normal operating temperature of the chip.
- Matching of Thermal Expansion Coefficients: Small-size LEDs are usually applied to devices with strict requirements for size and weight, such as wearable devices. In this case, the thermal expansion coefficient of the epoxy resin encapsulation material needs to match that of materials such as the chip and the substrate to avoid generating excessive stress when the temperature changes, which may lead to damage to the chip or the encapsulation structure.
Differences in Mechanical Performance
Mechanical Performance Requirements of High-Power LEDs
- High Hardness and Wear Resistance: High-power LEDs are often used in harsh environments such as outdoor lighting and industrial lighting, and may be subject to mechanical collisions and friction. Therefore, the epoxy resin encapsulation material needs to have high hardness and wear resistance to protect the LED chip from damage.
- Impact Resistance: During the installation and use of high-power LED lamps, they may be subject to a certain degree of impact force, such as vibrations during transportation and accidental collisions. The epoxy resin encapsulation should have good impact resistance and be able to withstand a certain degree of external impact without cracking to ensure the reliability of the LED.
Mechanical Performance Characteristics of Small-Size LEDs
- Flexibility and Bend Resistance: In some applications of flexible displays and wearable devices using small-size LEDs, the encapsulation material needs to have a certain degree of flexibility and bend resistance. The epoxy resin can improve its flexibility by adding special toughening agents and other means to adapt to the bending and deformation of the flexible substrate and protect the chip from damage at the same time.
- Encapsulation Precision at Small Sizes: The chip size of small-size LEDs is very small, and the requirements for encapsulation precision are extremely high. The epoxy resin encapsulation process needs to have high-precision control capabilities to ensure that the chip is accurately positioned during the encapsulation process and avoid problems such as offset and tilt to ensure the performance and reliability of the LED.
Differences in Encapsulation Processes
Encapsulation Processes of High-Power LEDs
- Fixation and Connection of High-Power Chips: The chips of high-power LEDs are usually large in size and high in power, and reliable fixation and connection methods need to be adopted. Common methods include silver paste die bonding and gold wire bonding to ensure good electrical connection and mechanical stability between the chip and the substrate.
- Potting Process: The encapsulation of high-power LEDs usually adopts the potting process, in which the epoxy resin is poured into the encapsulation mold to protect the chip and the internal circuit. During the potting process, the viscosity, fluidity, and curing conditions of the epoxy resin need to be controlled to avoid defects such as bubbles and voids, which will affect the encapsulation quality.
Encapsulation Processes of Small-Size LEDs
- Processing Technology for Tiny Chips: The chip size of small-size LEDs is very small, and the processing difficulty is relatively large. High-precision equipment and processes, such as high-precision die bonders and micro-assembly technologies, need to be adopted to achieve the accurate placement and fixation of the chip.
- Thin Film Encapsulation Technology: In order to meet the application requirements of small-size LEDs in some ultra-thin and lightweight devices, thin film encapsulation technology has gradually been applied. This technology realizes the protection and encapsulation of the chip by depositing one or more layers of thin films on the surface of the chip, which has the advantages of thin thickness and light weight.
Differences in Cost and Production Efficiency
Cost and Production Efficiency of High-Power LEDs
- Higher Cost: The encapsulation of high-power LEDs requires the use of high-performance epoxy resin materials, heat dissipation components, and complex encapsulation processes, so the cost is relatively high. In addition, the price of high-power LED chips is also relatively expensive, further increasing the overall cost.
- Relatively Lower Production Efficiency: Due to the relatively complex encapsulation process of high-power LEDs, strict quality control and inspection are required during the production process to ensure the performance and reliability of the products. This results in a longer production cycle for high-power LEDs and relatively lower production efficiency.
Cost and Production Efficiency of Small-Size LEDs
- Relatively Lower Cost: The chip size of small-size LEDs is small, and the required epoxy resin materials and other encapsulation materials are relatively less. At the same time, the encapsulation process is relatively simple, so the cost is relatively low. In addition, large-scale production of small-size LEDs can further reduce the cost.
- Higher Production Efficiency: The encapsulation process of small-size LEDs can achieve automated and large-scale production, with higher production efficiency. By adopting advanced production equipment and processes, such as high-speed die bonders and automated encapsulation production lines, the production efficiency can be greatly improved, and the production cost can be reduced.
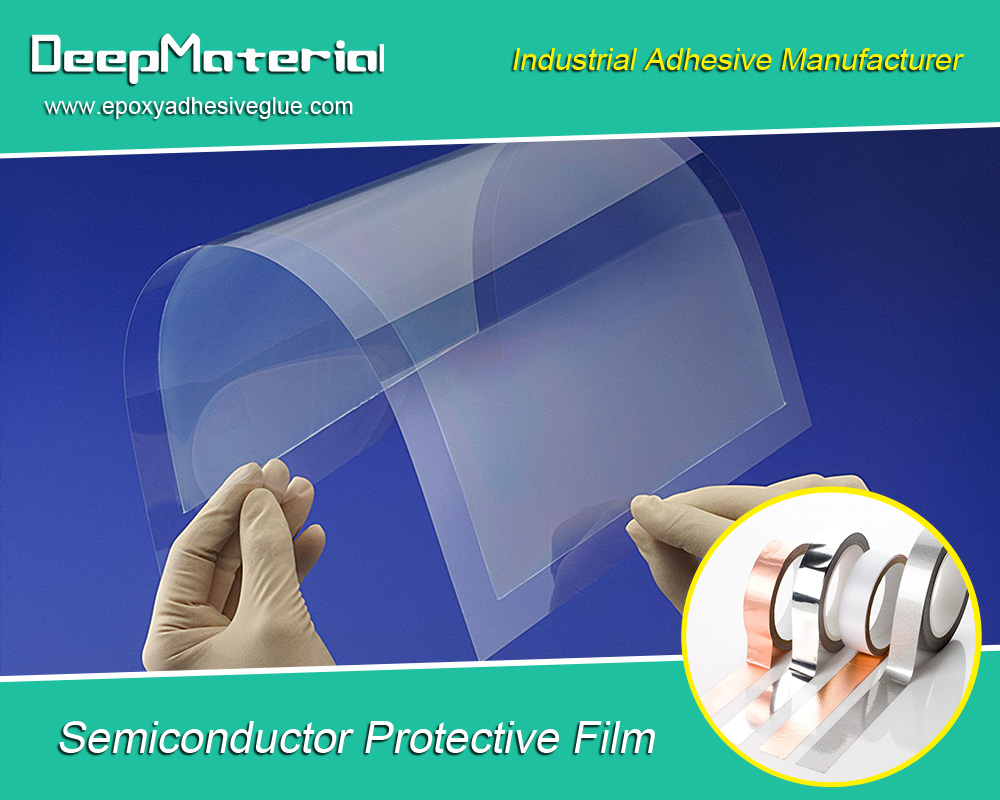
Conclusion
In conclusion, there are many differences in the epoxy resin encapsulation technology between high-power LEDs and small-size LEDs. In terms of optical performance, high-power LEDs focus on high light transmittance and precise optical design, while small-size LEDs emphasize high color purity and optical consistency. In terms of thermal performance, high-power LEDs have higher requirements for heat dissipation and thermal stability, while small-size LEDs pay more attention to the matching of thermal expansion coefficients. In terms of mechanical performance, high-power LEDs require high hardness and impact resistance, while small-size LEDs require flexibility and encapsulation precision. In terms of encapsulation processes, high-power LEDs adopt the fixation of high-power chips and the potting process, while small-size LEDs rely on the processing of tiny chips and thin film encapsulation technology. In terms of cost and production efficiency, high-power LEDs have high costs and low production efficiency, while small-size LEDs have low costs and high production efficiency.
Understanding these differences helps to select the appropriate LED type and encapsulation technology according to different needs in practical applications to achieve the best performance and economic benefits. At the same time, with the continuous development of LED technology, the epoxy resin encapsulation technology will also continue to innovate and improve to meet the application requirements of high-power LEDs and small-size LEDs in more fields. In the future, it is necessary to further strengthen the research on LED encapsulation technology and develop more high-performance and low-cost encapsulation materials and processes to promote the sustainable development of the LED industry.
For more about choosing the best analysis of the differences in epoxy resin encapsulation technology between high-power LEDs and small-size LEDs, you can pay a visit to DeepMaterial at https://www.epoxyadhesiveglue.com/category/epoxy-adhesives-glue/ for more info.