Characteristics of Epoxy Resin Used for LED Encapsulation and the Influence of the Encapsulation Effect
Characteristics of Epoxy Resin Used for LED Encapsulation and the Influence of the Encapsulation Effect
With the continuous development of LED technology, its applications in fields such as lighting and display are becoming increasingly widespread. Epoxy resin, as a commonly used LED encapsulation material, occupies an important position in LED encapsulation due to its good comprehensive properties, such as high insulation, good light transmittance, and appropriate mechanical strength. However, the performance of epoxy resin is closely related to its components, and different component proportions can significantly affect the encapsulation effect of LEDs. Therefore, in-depth research on the components and characteristics of epoxy resin as well as the influence of component proportions on the encapsulation effect is of great practical significance.
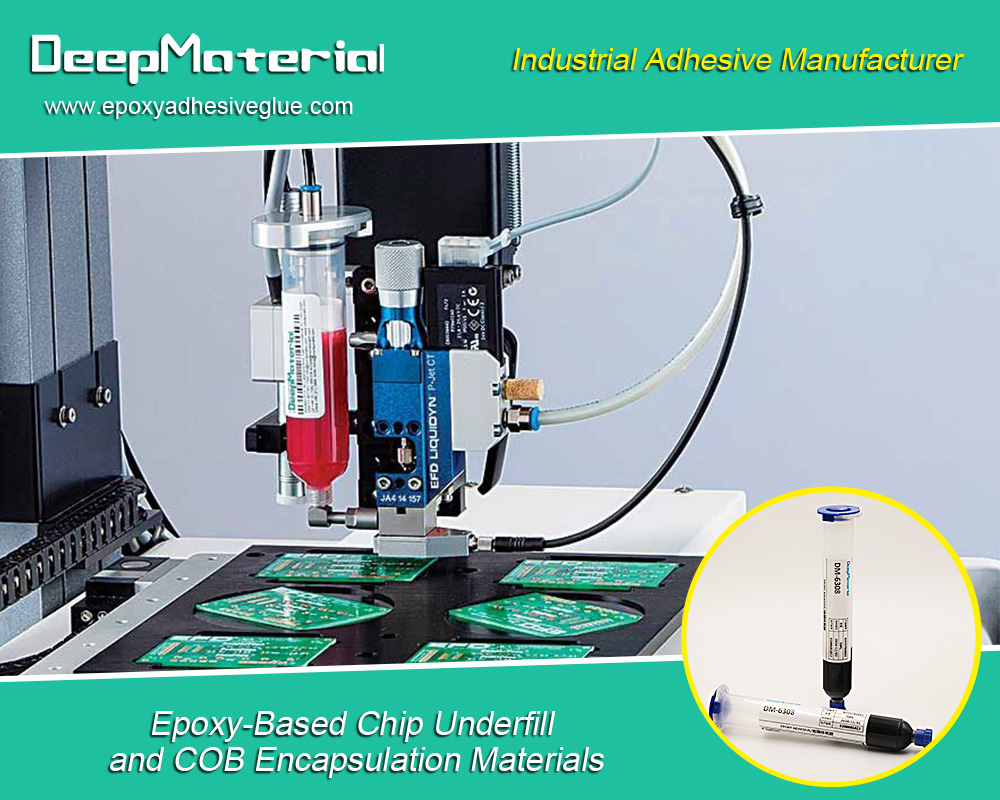
Main Components and Characteristics of Epoxy Resin Used for LED Encapsulation
Epoxy Resin Matrix
Epoxy resin is a polymer containing epoxy groups, which has good adhesion, insulation, and chemical corrosion resistance. In LED encapsulation, the commonly used epoxy resin is bisphenol A type epoxy resin. Its molecular structure contains two epoxy groups, which can undergo a cross-linking reaction under the action of a curing agent to form a three-dimensional network structure. The main characteristics of the epoxy resin matrix include:
- Adhesion: It can firmly bond the LED chip and other encapsulation components, ensuring the stability of the encapsulation structure.
- Insulation: It has a high insulation resistance, which can effectively prevent the occurrence of electrical leakage and ensure the safe operation of the LED.
- Chemical Corrosion Resistance: It has good resistance to common chemical substances and can protect the LED chip from chemical corrosion.
Curing Agent
The curing agent is a key component that causes the cross-linking reaction of the epoxy resin. Commonly used curing agents include amine curing agents, anhydride curing agents, etc. Different types of curing agents have different curing characteristics and reaction mechanisms.
- Amine Curing Agents: They react with the epoxy resin relatively quickly, and the cured product has high hardness and strength. However, amine curing agents have relatively large volatility, which has a certain impact on the health of operators.
- Anhydride Curing Agents: They react with the epoxy resin relatively slowly and require curing at a higher temperature. The cured product has good heat resistance and electrical insulation, and the volatility is relatively small.
Filler
The filler in the epoxy resin mainly plays the role of improving performance and reducing costs. Commonly used fillers include silica, aluminum oxide, etc.
- Silica: It has good chemical stability and insulation, which can improve the hardness and wear resistance of the epoxy resin. At the same time, the addition of silica can also reduce the shrinkage rate of the epoxy resin and reduce the stress generated during the encapsulation process.
- Aluminum Oxide: It has a high thermal conductivity, which can effectively improve the heat dissipation performance of the epoxy resin. In LED encapsulation, good heat dissipation performance is crucial for improving the service life and luminous efficiency of LEDs.
Additives
Additives include coupling agents, flame retardants, leveling agents, etc., which play a role in improving specific properties in the epoxy resin.
- Coupling Agents: They can enhance the interfacial bonding force between the epoxy resin and the filler, improving the performance of the composite material.
- Flame Retardants: In some application scenarios where fire prevention is required, the addition of flame retardants can improve the flame retardant performance of the epoxy resin.
- Leveling Agents: They can improve the fluidity and surface flatness of the epoxy resin, making the surface of the encapsulated LED smoother and improving the optical performance.
Influence of Different Component Proportions on the Encapsulation Effect
Influence on Optical Performance
- Proportion of Epoxy Resin Matrix and Curing Agent: Different proportions will affect the refractive index and transparency of the cured product. When the proportion of the epoxy resin matrix and the curing agent is appropriate, the cured product has high transparency and a suitable refractive index, which can effectively transmit and refract light and improve the luminous efficiency of the LED. If the proportion is not appropriate, the cured product may be turbid or have a refractive index deviation, thus affecting the optical performance of the LED.
- Filler Proportion: The addition of filler will change the optical properties of the epoxy resin. For example, the addition of silica filler will change the refractive index of the epoxy resin, thus affecting the propagation path of light. An appropriate amount of silica filler can improve the light transmittance of the epoxy resin, but an excessive amount of filler may lead to an increase in light scattering and a decrease in light transmittance. Although the main function of aluminum oxide filler is to improve the heat dissipation performance, it will also have a certain impact on the optical performance. Too much aluminum oxide filler may reduce the transparency of the epoxy resin.
- Additive Proportion: The addition of some additives such as leveling agents can improve the surface flatness of the epoxy resin, reduce light reflection and scattering, and improve the optical performance. The addition of flame retardants may have a certain negative impact on the light transmittance of the epoxy resin, so it is necessary to balance the flame retardant performance and optical performance.
Influence on Thermal Performance
- Proportion of Epoxy Resin Matrix and Curing Agent: An appropriate proportion can make the epoxy resin cure fully and form a dense cross-linked structure, improving the thermal stability. If the proportion is not appropriate, it may lead to incomplete curing, with unreacted groups remaining, thus reducing the thermal stability and affecting the heat dissipation performance of the LED.
- Filler Proportion: The addition of thermal conductive fillers such as aluminum oxide can significantly improve the thermal conductivity of the epoxy resin. As the filler proportion increases, the thermal conductivity gradually increases. However, when the filler proportion is too high, it will lead to poor fluidity of the epoxy resin, which is not conducive to the implementation of the encapsulation process, and may also affect other properties. Therefore, it is necessary to select an appropriate filler proportion to achieve the best heat dissipation effect.
- Additive Proportion: The addition of coupling agents can enhance the interfacial bonding force between the epoxy resin and the filler, improving the heat conduction efficiency. Some additives may have an impact on the thermal expansion coefficient of the epoxy resin, thus affecting the performance stability of the LED in different temperature environments.
Influence on Mechanical Performance
- Proportion of Epoxy Resin Matrix and Curing Agent: When the proportion is appropriate, the cured product has high hardness, strength, and toughness. If there is too much epoxy resin matrix, the cured product may be relatively soft and have insufficient strength; while if there is too much curing agent, the cured product may be too brittle and have reduced toughness.
- Filler Proportion: An appropriate amount of filler can improve the hardness and wear resistance of the epoxy resin, but an excessive amount of filler will reduce the toughness of the epoxy resin and make it prone to cracking. For example, the addition of silica filler can increase the hardness of the epoxy resin, but when the filler proportion is too high, the brittleness of the material increases, and it is easily damaged when subjected to external impact.
- Additive Proportion: Coupling agents can enhance the interfacial bonding force between the epoxy resin and the filler, thereby improving the mechanical properties of the composite material. The influence of additives such as leveling agents on the mechanical properties is relatively small, but if used improperly, it may affect the curing quality of the epoxy resin and thus affect the mechanical properties.
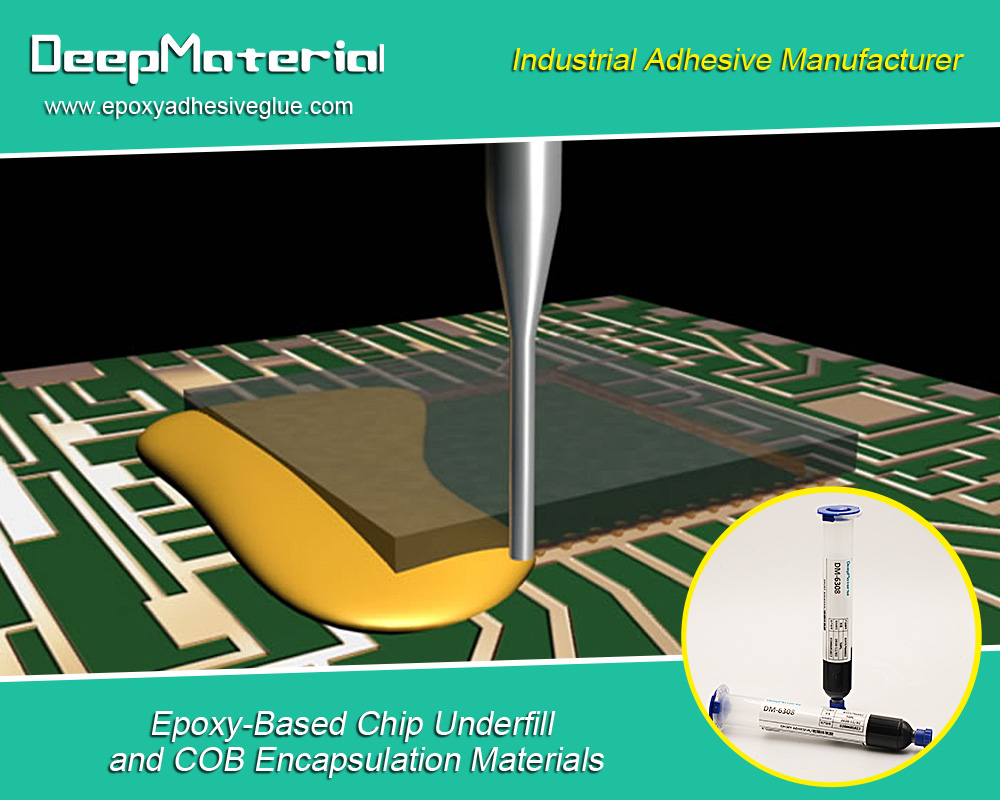
Conclusion
The main components of epoxy resin used for LED encapsulation include the epoxy resin matrix, curing agent, filler, and additives, etc. Each component has different characteristics, and they interact with each other to jointly determine the performance of the epoxy resin. Different component proportions have a significant impact on the LED encapsulation effect in terms of optical performance, thermal performance, and mechanical performance. In order to obtain the best encapsulation effect, it is necessary to accurately control the proportions of each component of the epoxy resin according to the specific application requirements of the LED and optimize the encapsulation process. In the future, with the continuous development of LED technology, the performance requirements for epoxy resin encapsulation materials will also continue to increase. Further in-depth research on the components and characteristics of epoxy resin as well as the influence of component proportions on the encapsulation effect is of great significance for promoting the development of the LED industry. At the same time, the development of new epoxy resin encapsulation materials and the optimization of the performance of existing materials are also one of the future research directions.