Low Temperature Epoxy Adhesive: A Comprehensive Guide to Applications, Advantages, and Best Practices
Low Temperature Epoxy Adhesive: A Comprehensive Guide to Applications, Advantages, and Best Practices
Epoxy adhesives have long been a staple in industries requiring robust and reliable bonding solutions. However, when operating in environments where high temperatures are not feasible, specialized products like low temperature epoxy adhesives come into play. These adhesives are engineered to provide exceptional bonding strength at temperatures significantly lower than traditional epoxies, offering flexibility for industries and projects that need to work under specific conditions.
This article will explore the characteristics, benefits, and applications of Low temperature epoxy adhesives and some best practices to ensure their optimal performance. This guide will provide valuable insights if you’re seeking an adhesive solution that excels even in challenging cold environments.
What is Low Temperature Epoxy Adhesive?
Low temperature epoxy adhesives are specially formulated to cure at lower temperatures, typically below ten °C (50°F), making them suitable for environments where conventional epoxies might fail to bond effectively. These adhesives maintain the desirable properties of epoxy—such as high strength, resistance to environmental factors, and versatility—but are modified to provide effective bonding under cooler conditions.
Key Features:
- They are curing at low temperatures (as low as -40°C sometimes).
- Retains bonding strength and structural integrity in more relaxed environments.
- Excellent chemical and environmental resistance.
- Versatile usage across multiple materials like metals, plastics, composites, and ceramics.
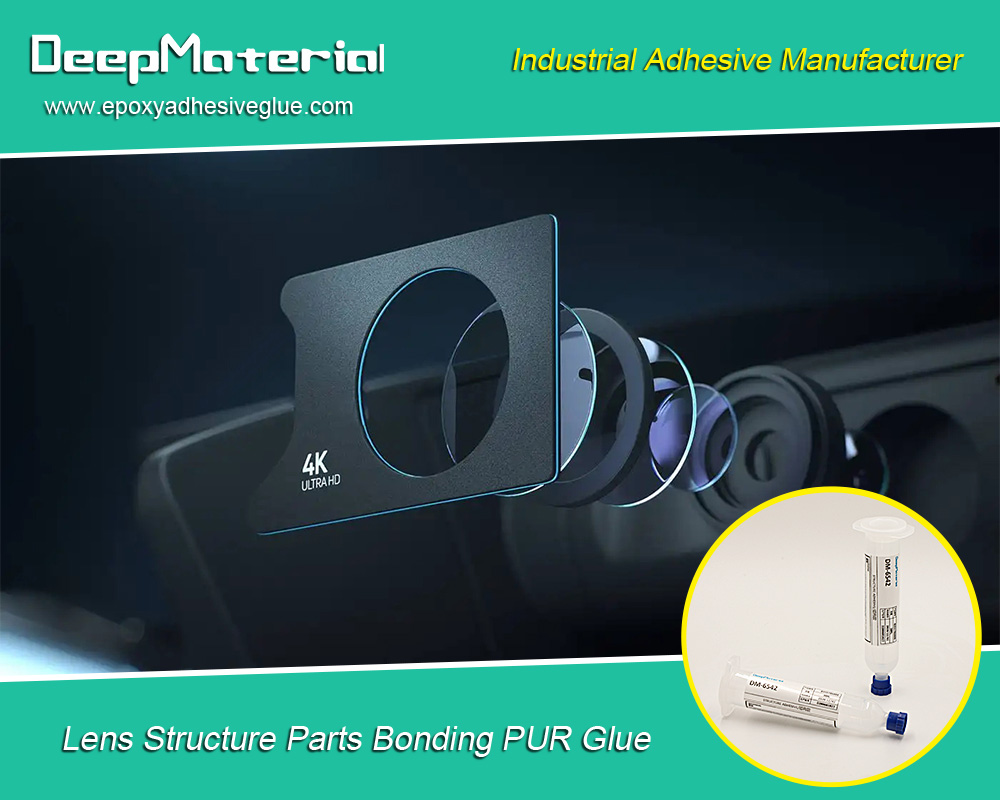
Critical Applications of Low Temperature Epoxy Adhesive
Aerospace Industry
- Structural bonding for aircraft: These adhesives are essential for bonding components in aircraft manufacturing, especially when components are exposed to high altitudes and freezing temperatures.
- Satellite and space exploration equipment: In aerospace, satellites, and spacecraft must endure extreme temperature fluctuations. Low temperature epoxy adhesives are critical for maintaining the structural integrity of these components.
Automotive Industry
- Cold-weather vehicle assembly: Car manufacturers use Low temperature epoxies to assemble vehicles designed for colder climates. These adhesives bond materials even in unheated environments, maintaining durability despite temperature fluctuations.
- Battery component bonding: Electric cars rely on specialized adhesives to hold together battery components that operate in various temperatures, including cold starts.
Electronics and Semiconductor Manufacturing
- Cold-soldering applications: These adhesives are vital for assembling electronics exposed to low temperatures, especially when standard soldering isn’t possible.
- Bonding of delicate components: Low temperature epoxies provide precise bonding solutions for microelectronic components that cannot withstand high heat during assembly.
Construction and Civil Engineering
- Cold weather construction:Infrastructure projects in more frigid climates demand adhesives that can cure at low temperatures for tasks like joint bonding, crack repair, or panel assembly.
- Bridge and road repair:For structures exposed to extreme cold, such as bridges in northern regions, low temperature epoxies are used to repair cracks and stabilize structural components.
Marine Applications
- Shipbuilding:These adhesives are essential in shipbuilding, especially for bonding metal parts exposed to water and cold environments.
- Cold-water pipelines and infrastructure: Pipelines transporting cold water or oil in Arctic regions utilize these adhesives to ensure long-lasting structural integrity.
Advantages of Using Low Temperature Epoxy Adhesive
Improved Workability in Cold Conditions
- Low temperature epoxy adhesives enable operations in cold environments where other adhesives would either cure too slowly or not.
- This adhesive minimizes delays caused by environmental factors, allowing workers to perform bonding tasks in colder seasons or unheated spaces.
Versatile Compatibility with Multiple Substrates
- These adhesives bond effectively to various materials, including metals, plastics, ceramics, and composites, providing flexibility across different industries.
- They allow seamless adhesion between substrates with varying expansion and contraction rates, making them ideal for temperature-sensitive materials.
Longer Shelf Life
- Due to their specialized formulations, Low temperature epoxy adhesives tend to have longer shelf lives than traditional epoxies. This makes them more cost-effective for companies needing to store adhesive materials over extended periods.
High Chemical Resistance
- These adhesives provide robust resistance against chemicals, including oils, solvents, and acids, making them suitable for harsh environments such as industrial plants, offshore platforms, and chemical processing facilities.
Structural Durability
- Even when exposed to cold environments, these adhesives maintain their mechanical properties, offering exceptional strength, flexibility, and durability. It ensures bonded components perform consistently over time, even under mechanical stresses or environmental factors like moisture and frost.
Selecting the Right Low Temperature Epoxy Adhesive
Choosing the suitable low temperature epoxy adhesive for your project depends on several factors. Here are some important considerations to guide you:
- Temperature Range: Ensure the adhesive can cure within the specific temperature range required for your application. Some adhesives are designed to function in icy environments, while others perform better at moderately low temperatures.
- Material Compatibility: Match the adhesive to the materials you’re bonding. Not all low temperature epoxies are suitable for all materials, so check for compatibility with metals, plastics, or composites.
- Cure Time: Consider how quickly the adhesive needs to cure. If you work in time-sensitive conditions, faster-curing adhesives might be required. However, extended working times can be advantageous for more precise applications.
- Viscosity: Select an adhesive with a viscosity that suits the application method (e.g., brushing, pouring, or injecting). Thicker adhesives may be necessary for vertical or overhead applications to prevent sagging.
- Environmental Exposure: If the adhesive will be used in outdoor or industrial settings, evaluate its resistance to moisture, UV rays, and chemicals.
Best Practices for Application and Curing
Achieving the best results from low temperature epoxy adhesives requires careful attention to the application process. Below are some best practices to ensure optimal bonding and curing:
- Surface Preparation: Clean the surfaces thoroughly to remove dirt, oils, and contaminants. Roughen the surfaces slightly to increase the adhesive’s grip, especially on smooth materials like metals or plastics.
- Preheating Components: While low temperature epoxy adhesives cure at cooler temperatures, slightly preheating the materials can speed up the curing process and improve bond strength, particularly in freezing conditions.
- Mixing Ratios:Ensure precise mixing ratios between the resin and hardener components. Inaccurate measurements may affect the adhesive’s strength and curing time.
- Apply Even Pressure: When bonding materials, apply even pressure to ensure a uniform bond and avoid air bubbles or gaps between surfaces.
- Allow Full Curing Time: Be patient and allow the adhesive to cure fully before putting the bonded components into service. Even though these adhesives are designed to heal in colder environments, rushing the curing process can compromise the bond’s strength.
Comparison Between Low Temperature Epoxy Adhesive and Traditional Epoxies
Curing Time:
- Low temperature epoxies are designed to cure faster at lower temperatures, whereas traditional epoxies require warmer conditions to heal effectively.
Bonding Strength:
- While both types offer high bonding strength, low temperature epoxy adhesives maintain better flexibility and structural integrity when exposed to freezing temperatures. Traditional epoxies can become brittle in cold environments.
Application Versatility:
- Low temperature epoxies excel in colder climates and environments, but traditional epoxies are often better suited for applications that require high heat resistance.
Cost:
- Low temperature epoxies may have a slightly higher cost due to their specialized formulations, but they offer unique advantages in terms of performance and long-term durability in cold conditions.
Challenges and Limitations
While low temperature epoxy adhesives offer many benefits, they also come with specific challenges and limitations:
- Longer Cure Times in Extreme Cold: While designed for cold environments, curing time may extend when temperatures are significantly below freezing.
- Limited Use in High-Heat Environments: These adhesives may perform poorly in high-temperature environments, as their formulations are optimized for cold conditions.
- More Specialized Handling Requirements: Handling and storing Low temperature epoxies often require specific environmental controls, which can complicate their use in certain situations.
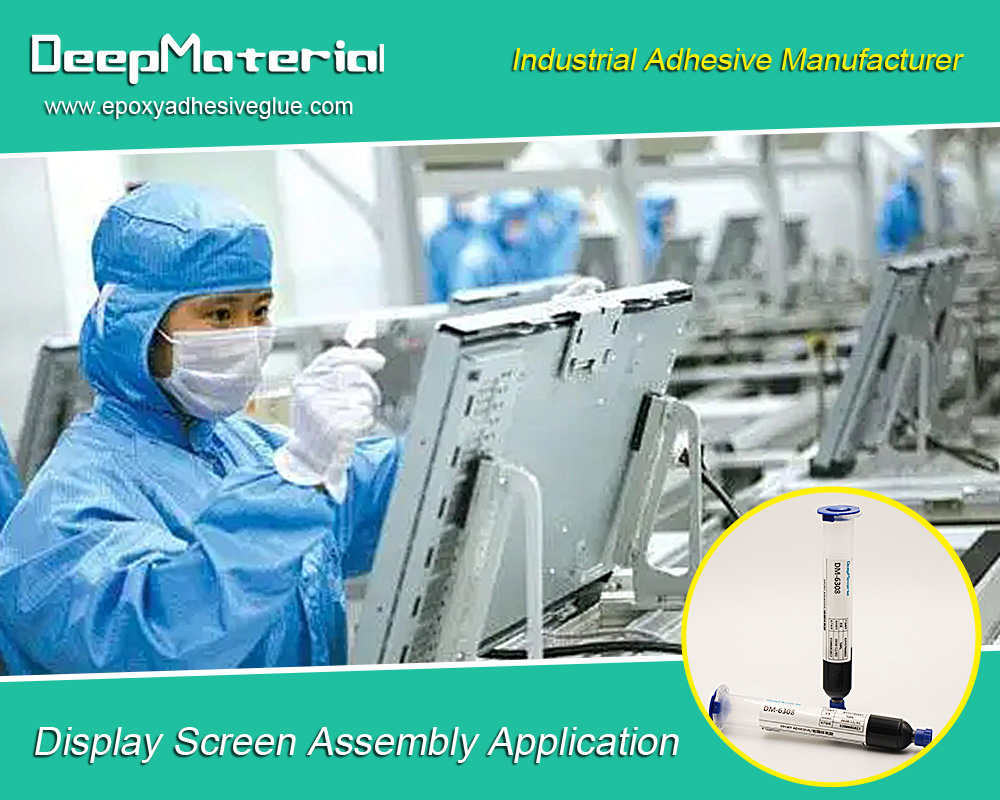
Conclusion
Low temperature epoxy adhesives represent a critical advancement in bonding technology for industries and applications operating in cold or controlled environments. Whether in aerospace, automotive, electronics, or construction, these adhesives offer a reliable solution for ensuring strong, durable bonds where conventional adhesives fall short.
By understanding their unique properties, benefits, and best practices, businesses and engineers can fully take advantage of Low temperature epoxy adhesives, ensuring optimal performance even in the most challenging environments. As technology continues to evolve, we can expect further innovations that make these adhesives even more versatile, environmentally friendly, and efficient.
For more about choosing the best low temperature epoxy adhesive: a comprehensive guide to applications, advantages, and best practices, you can pay a visit to DeepMaterial at https://www.epoxyadhesiveglue.com/category/epoxy-adhesives-glue/ for more info.