Methods for Ensuring Uniform Encapsulation of LED Chips with Epoxy Resin, Process Difficulties and Solutions
Methods for Ensuring Uniform Encapsulation of LED Chips with Epoxy Resin, Process Difficulties and Solutions
With the rapid development of LED technology, it has been widely used in many fields such as lighting, display, automotive electronics, etc. Epoxy resin, as a commonly used encapsulation material for LEDs, has good optical, insulating and mechanical properties. However, it is not an easy task to achieve uniform encapsulation of LED chips with epoxy resin, which is directly related to key performance indicators of LEDs, such as luminous uniformity, heat dissipation performance and long-term stability. Therefore, it is of great practical significance to study how to ensure the uniform encapsulation of LED chips with epoxy resin and solve related process difficulties.
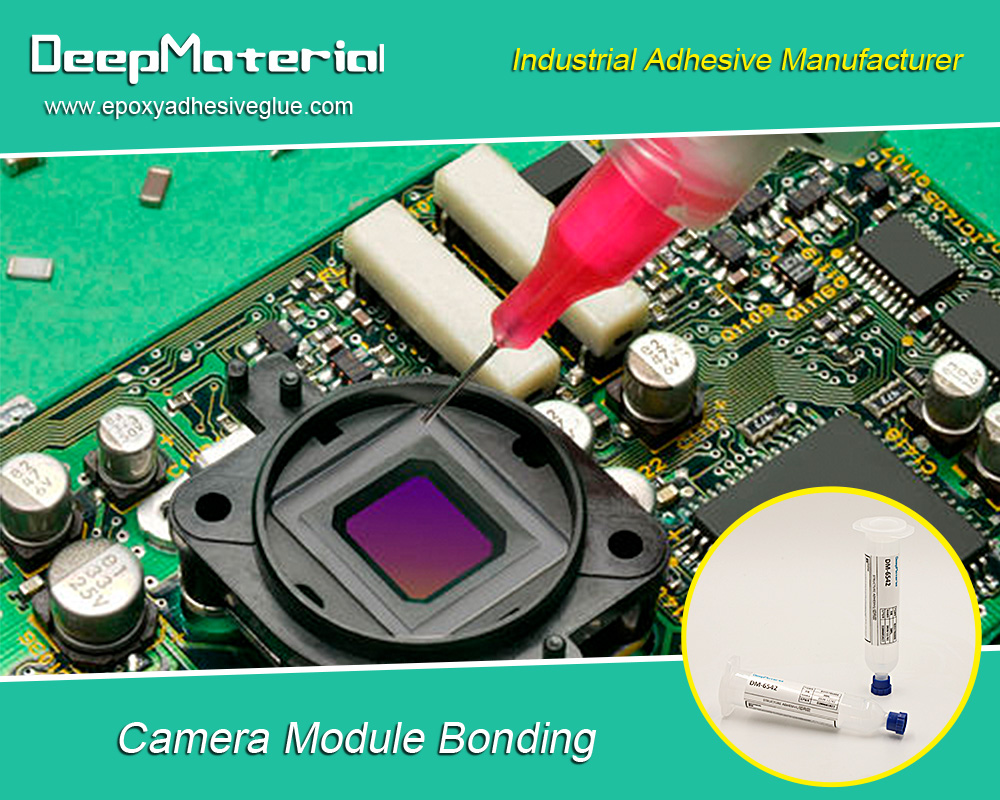
Methods for Ensuring Uniform Encapsulation of LED Chips with Epoxy Resin
(1) Precise Bracket Design
- Reasonable Chip Placement Area
When designing the bracket, the shape and size of the chip placement area should be matched with the LED chip, and the surface should be flat and smooth. This enables the epoxy resin to flow evenly around the chip during the pouring process, avoiding local accumulation or voids. For example, use high-precision molds to manufacture the bracket to ensure that the dimensional accuracy of the chip placement area is within a very small tolerance range.
- Design of Drainage Structure
Set up drainage grooves or holes and other structures on the bracket to guide the flow direction of the epoxy resin, enabling it to encapsulate the chip more uniformly. These drainage structures can be optimized according to the shape and position of the chip to ensure that the epoxy resin can smoothly cover all parts of the chip.
(2) Precise Control of the Pouring Process
- Selection of Dispensing or Pouring Equipment
Use high-precision dispensing machines or pouring equipment, which can accurately control the pouring amount and speed of the epoxy resin. For example, a screw-type dispensing machine has high-precision metering and control functions, enabling micro and uniform pouring of the epoxy resin. At the same time, the design of the nozzle of the equipment is also crucial. An appropriate nozzle shape and size can make the epoxy resin flow out at a uniform flow rate.
- Planning of the Pouring Path
According to the structure of the chip and the bracket, plan a reasonable pouring path. Multi-point pouring or point-by-point pouring methods can be adopted to ensure that the epoxy resin flows evenly towards the chip from different directions. During the pouring process, pay attention to the pouring sequence and time interval to avoid excessive accumulation or poor flow of the epoxy resin in a certain area.
(3) Degassing Treatment
- Vacuum Degassing
After the epoxy resin is mixed, put it into a vacuum degassing machine for degassing treatment. In a vacuum environment, the bubbles in the epoxy resin will rise and burst due to the internal and external pressure difference, thus removing the bubbles. The degassing time and vacuum degree need to be adjusted reasonably according to the characteristics and dosage of the epoxy resin. Generally, the vacuum degree is controlled between -0.08MPa and -0.1MPa, and the degassing time is 10 – 20 minutes.
- Centrifugal Degassing
In addition to vacuum degassing, centrifugal degassing can also be used. Put the mixed epoxy resin into a centrifugal device, and the centrifugal force generated by high-speed rotation makes the bubbles concentrate on the surface of the epoxy resin, and then remove the surface layer containing bubbles. The speed and time of centrifugal degassing also need to be optimized according to the actual situation.
(4) Control of the Curing Process
- Uniform Temperature Distribution
During the curing process, it is essential to ensure a uniform temperature distribution in the curing furnace. A high-precision temperature control system and a good heat conduction design can be used to enable the epoxy resin to be uniformly heated during the curing process. For example, use a curing furnace with a hot air circulation system, which can make the temperature in the furnace more uniform and avoid uneven curing of the epoxy resin due to excessively high or low local temperatures.
- Appropriate Curing Speed
Controlling the curing speed can also affect the uniform encapsulation effect of the epoxy resin. Too fast a curing speed may cause the epoxy resin to cure before it has fully flowed and encapsulated the chip, while too slow a curing speed will affect production efficiency. According to the formulation and characteristics of the epoxy resin, select an appropriate curing temperature curve and time to enable the epoxy resin to complete the curing process within an appropriate time and uniformly encapsulate the chip.
Common Process Difficulties
(1) Bubble Problem
- Causes of Bubble Generation
Bubbles may be generated during the mixing, pouring and curing processes of the epoxy resin. For example, uneven stirring during the mixing process will introduce air and form bubbles; too fast a pouring speed or improper pouring method will also bring air into the epoxy resin; in addition, the surface tension and viscosity characteristics of the epoxy resin itself will also affect the generation and removal of bubbles.
- Impact of Bubbles on Uniform Encapsulation
The presence of bubbles will destroy the uniformity of the epoxy resin, resulting in voids or cavities around the chip, affecting the optical performance and heat dissipation performance of the LED. At the same time, the bubbles may expand or burst during the curing process, further affecting the encapsulation effect and encapsulation quality of the epoxy resin.
(2) Fluidity Problem of Epoxy Resin
- Reasons for Insufficient Fluidity
The fluidity of the epoxy resin is affected by many factors, such as temperature, viscosity, formulation, etc. If the viscosity of the epoxy resin is too high, it will be difficult to flow evenly around the chip during the pouring process, resulting in uneven encapsulation. In addition, too low an ambient temperature will also reduce the fluidity of the epoxy resin, making it difficult to fully fill the gaps between the chip and the bracket.
- Challenges of Fluidity to Uniform Encapsulation
Insufficient fluidity will cause the epoxy resin to form local accumulation around the chip or fail to completely cover the chip. This problem is more prominent especially for some chips or brackets with complex structures. This will not only affect the optical performance of the LED, but also lead to uneven bonding force between the chip and the epoxy resin, reducing the reliability of the encapsulation.
(3) Chip Position Deviation
- Reasons for Position Deviation
During the pouring process of the epoxy resin, the chip may deviate from its position due to the impact force of the liquid or the surface tension. In addition, the curing shrinkage or unevenness of the die bonding adhesive during the die bonding process may also cause the position change of the chip.
- Impact of Position Deviation on Uniform Encapsulation
The deviation of the chip position will cause the epoxy resin to be unevenly encapsulated around the chip. It may lead to the epoxy resin being too thick in some parts and too thin or even unable to cover in other parts. This will seriously affect the optical and electrical performance of the LED and reduce the consistency and reliability of the product.
(4) Uneven Curing of Epoxy Resin
- Reasons for Uneven Curing
Uneven curing may be caused by uneven temperature distribution in the curing furnace, uneven formulation of the epoxy resin or improper control of the curing speed. In addition, the difference in thermal conductivity between the chip and the bracket may also lead to different curing speeds of the epoxy resin in different parts.
- Consequences of Uneven Curing for Uniform Encapsulation
Uneven curing will make the epoxy resin form different hardness and density around the chip, affecting its protective and supporting effects on the chip. At the same time, it may also lead to inconsistent bonding force between the epoxy resin and the chip and the bracket, and problems such as cracking or peeling are likely to occur during long-term use.
Solutions
(1) Solutions to the Bubble Problem
- Optimize the Mixing Process
When mixing the epoxy resin, use an appropriate stirring method and speed to ensure that the epoxy resin is fully mixed without introducing too much air. A method of low-speed stirring and extending the stirring time can be adopted, and try to avoid violent stirring actions during the stirring process. In addition, the components of the epoxy resin can be preheated before mixing to reduce its viscosity and improve the mixing effect.
- Improve the Pouring Process
When pouring the epoxy resin, control the pouring speed to avoid bringing air in due to too fast pouring. A slow and uniform pouring method can be adopted, and pause appropriately during the pouring process to allow the epoxy resin to flow fully and discharge the bubbles. At the same time, select appropriate pouring equipment and nozzles to ensure that the epoxy resin can flow smoothly around the chip.
- Strengthen the Degassing Treatment
In addition to the previously mentioned vacuum degassing and centrifugal degassing, an appropriate amount of defoamer can also be added to the epoxy resin. The defoamer can reduce the surface tension of the epoxy resin, making it easier for the bubbles to burst and be removed. However, pay attention to the amount of defoamer added, as too much defoamer may affect the performance of the epoxy resin.
(2) Solutions to the Fluidity Problem of Epoxy Resin
- Adjust the Epoxy Resin Formulation
Adjust the formulation of the epoxy resin to reduce its viscosity and improve its fluidity. An appropriate amount of diluent can be added or a low-viscosity epoxy resin matrix can be selected. But when adjusting the formulation, pay attention to maintaining the other properties of the epoxy resin, such as optical, mechanical and curing properties.
- Control the Ambient Temperature
Before pouring the epoxy resin, preheat the epoxy resin and the encapsulation environment to an appropriate temperature to improve the fluidity of the epoxy resin. Generally speaking, an increase in temperature will reduce the viscosity of the epoxy resin and increase its fluidity. But pay attention to controlling the temperature within a reasonable range to avoid premature curing or performance degradation of the epoxy resin due to too high a temperature.
- Optimize the Bracket Structure
Optimize the structure of the bracket to reduce the resistance to the flow of the epoxy resin. For example, reduce the sharp corners and protrusions on the bracket to enable the epoxy resin to flow more smoothly. At the same time, some auxiliary flow structures, such as diversion grooves or holes, can be set on the bracket.
(3) Solutions to the Chip Position Deviation Problem
- Improve the Die Bonding Process
Improve the precision and stability of the die bonding process to ensure that the chip is firmly fixed on the bracket. Use high-precision die bonders and high-quality die bonding adhesives, control the dispensing amount and position of the die bonding adhesive, and ensure the accurate position of the chip before pouring the epoxy resin. In addition, appropriate curing treatment can be carried out after die bonding to enhance the strength of the die bonding adhesive and prevent the chip from deviating during subsequent processes.
- Optimize the Pouring Process
When pouring the epoxy resin, control the pouring speed and direction to reduce the impact force of the liquid on the chip. Multi-point pouring or step-by-step pouring methods can be adopted to make the epoxy resin evenly distributed around the chip and avoid chip deviation caused by excessive local pressure. At the same time, the angle of the bracket can be appropriately adjusted during the pouring process to enable the epoxy resin to flow more naturally around the chip.
(4) Solutions to the Uneven Curing Problem of Epoxy Resin
- Optimize the Curing Equipment
Use high-precision curing equipment to ensure a uniform temperature distribution in the curing furnace. A curing furnace with a temperature sensor and a feedback control system can be used to monitor and adjust the temperature in the furnace in real time. At the same time, regularly maintain and calibrate the curing equipment to ensure the accuracy of its temperature control.
- Adjust the Epoxy Resin Formulation
Optimize the formulation of the epoxy resin to make its curing reaction more uniform. A curing agent with a relatively stable curing speed can be selected, and the amount of the curing agent can be reasonably adjusted. In addition, some additives that promote uniform curing, such as latent curing agents or coupling agents, can also be added.
- Control the Curing Process
During the curing process, strictly control the curing temperature and time, and operate according to the curing curve of the epoxy resin. A segmented curing method can be adopted, first carry out pre-curing at a lower temperature to enable the epoxy resin to be initially cured and form a certain strength, and then carry out complete curing at a higher temperature to ensure that the epoxy resin is uniformly cured around the chip.
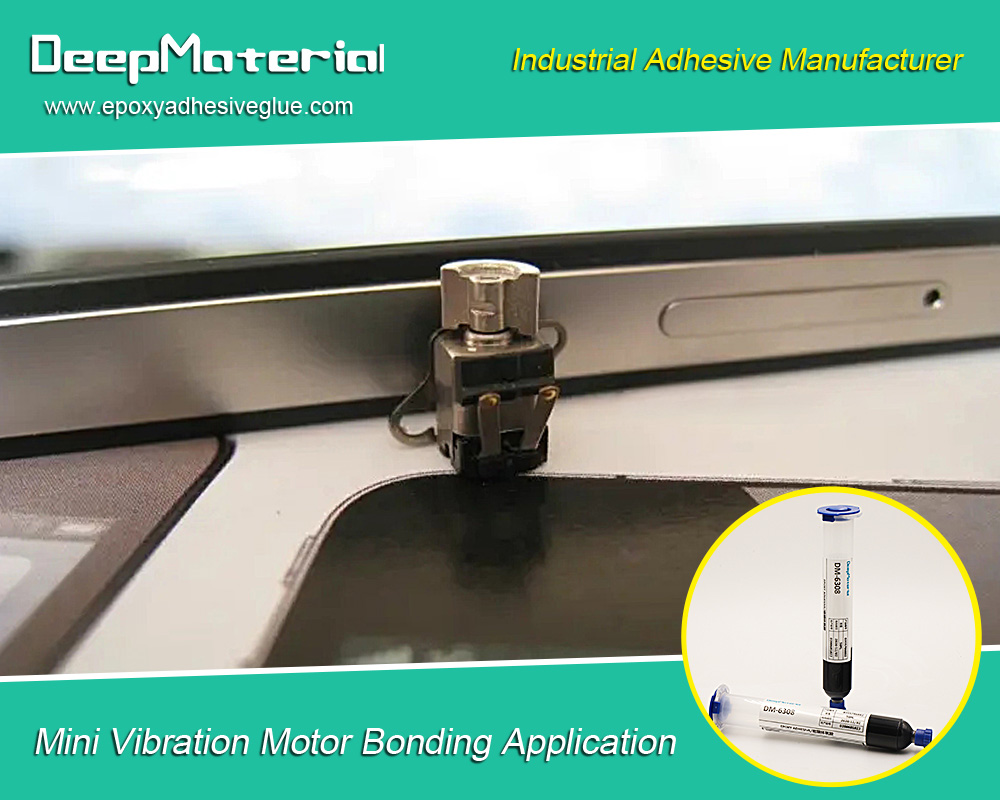
Conclusion
Ensuring the uniform encapsulation of LED chips with epoxy resin is a key link in the LED encapsulation process, which directly affects the performance and reliability of LEDs. Through methods such as precise bracket design, control of the pouring process, degassing treatment and control of the curing process, the uniformity of epoxy resin encapsulation can be effectively improved. At the same time, for common process difficulties, such as bubble problems, fluidity problems of epoxy resin, chip position deviation and uneven curing, corresponding solutions can be adopted to further improve the encapsulation quality. In actual production, it is necessary to continuously optimize the encapsulation process and strengthen quality control to meet the market demand for high-quality LED products and promote the sustainable development of the LED industry. In the future, with the continuous progress of LED technology and the continuous expansion of application fields, the requirements for the epoxy resin encapsulation process will become higher and higher. Continuous technological innovation and research are needed to adapt to the development needs of the industry.
For more about choosing the best epoxy adhesive glue for metal to plastic, you can pay a visit to DeepMaterial at https://www.epoxyadhesiveglue.com/category/epoxy-adhesives-glue/ for more info.