The Role of Membrane Bonding Adhesive in Robust Assembly
The Role of Membrane Bonding Adhesive in Robust Assembly
Membrane bonding adhesives have suddenly risen to prominence because of their unique ability to guarantee functionality, reliability, and structural integrity for components assembly. This adhesive plays an important role in ensuring permanent bonding. Its secure bond forming abilities has made it a preferred option for adherence for a wide range of applications.
In this post, we take a comprehensive look at the role of membrane bonding adhesives in electronics components assembly. We examine the benefits and challenges associated with using such adhesives. Also, we’ll consider the various applications that employ membrane bonding adhesive technology. This post will be shedding light on the ways in which membrane bonding adhesive contributes to creating robust and reliable assemblies across various sectors.
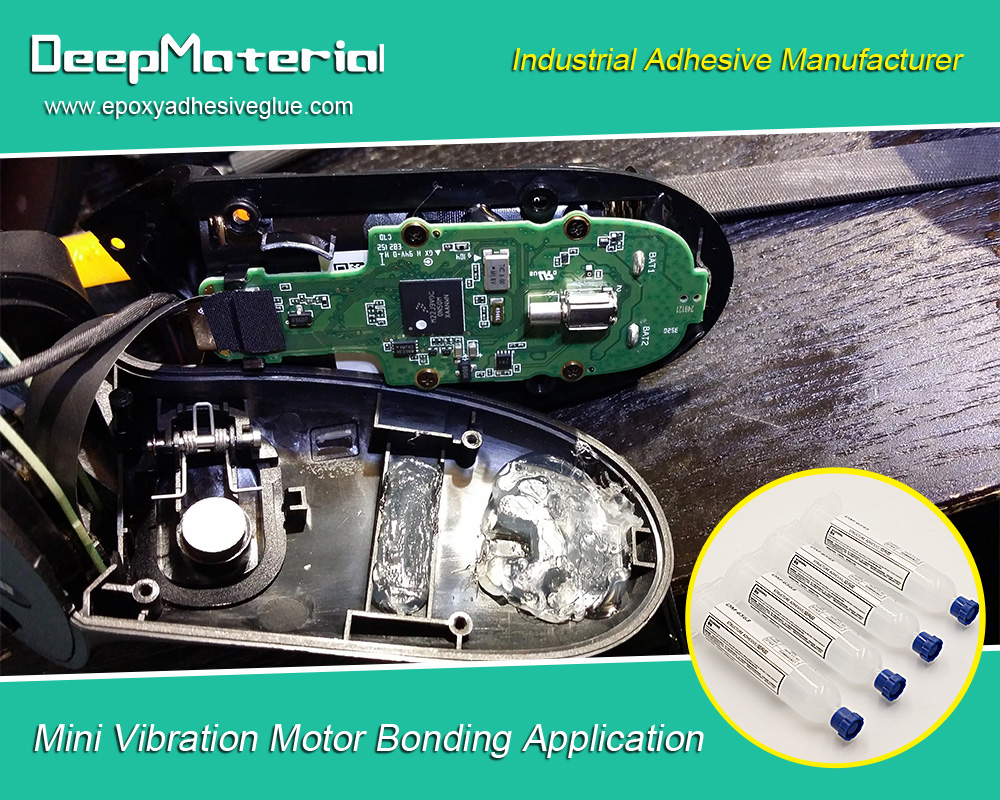
Membrane Bonding Adhesives Explained
This adhesive type is specifically formulated for securing, sealing, and bonding membranes usually employed in various industries. From the medical devices industry to the electronics industry, membrane bonding adhesive is used to accomplish one thing or the other.
In other words, this adhesive helps to ensure that the functionality and integrity of membranes are maintained during and after components assembly.
Membrane bonding adhesive is formulated to adhere to and seal membranes, creating a strong, durable, and reliable bond. Its primary function is to securely attach and seal membranes to other components or surfaces, preventing the ingress of contaminants, fluids, or gases and enhancing the overall performance and longevity of the assembly.
This adhesive acts as a protective barrier, maintaining the integrity of the membrane and preventing it from delaminating or detaching.
Characteristics and Properties of Membrane Bonding Adhesives
A reliable membrane bonding adhesive should possess certain qualities that will make them fit for such applications. If you seek the best membrane bonding adhesives, consider the properties below;
- Flexibility – They possess flexibility to accommodate the movement or deformation of the membranes without compromising the bond.
- Adhesion Strength – This adhesive produces a strong bond on different membranes, ensuring long-lasting bonds.
- Temperature Resistant Abilities – They can withstand a wide range of temperatures, ensuring stability in diverse operating conditions.
- Chemical Resistant Abilities – Membrane bonding adhesives have the ability to resist various chemicals. They offer protection to membranes by not reacting to many chemicals or unfavorable environmental conditions.
- Optical Clarity – In certain applications, optical clarity is essential to maintain the transparency of membranes, allowing for optical or visual inspections.
- Curing Mechanism – Membrane adhesives are meant to cure differently, depending on their chemical formulations. Some require chemicals to cure, while others require ultraviolet light to do the same. What is common is that the curing process is simple and straightforward for all of them.
These properties collectively contribute to the effectiveness of membrane bonding adhesive in achieving robust and reliable membrane assemblies, making it a valuable component in various industries.
How Membrane Bonding Adhesives Enhances Reliability
Membrane bonding adhesives are fast-becoming the go-to solution for membrane bonding due to their ability to guarantee reliability.
Membrane bonding adhesive offers a range of advantages and benefits that enhance assembly reliability and make it a preferred choice for various applications across industries. Highlighted below is how such adhesives enhances assembly reliability;
- Vibration and Shock Resistance – Membrane adhesive’s flexibility and durability allow it to absorb vibrations and shocks, ensuring the membrane remains in place even in dynamic environments.
- Sealing Capability – Membrane bonding adhesives are designed to provide effective sealing, not allowing liquids or any other contaminants to access the unit. Allowing such to happen can damage the assembly.
- Secure Bonding – Membrane bonding adhesive provides a strong and secure bond between the membrane and other components, reducing the risk of delamination or detachment during operation.
- Chemical Protection – The ability of this adhesive to protect an assembly from solvents and chemicals help to preserve assembly integrity.
What Are the Advantages of Using Membrane Bonding Adhesives?
Membrane bonding adhesives are formulated to serve the purpose of ensuring secure bonding in membrane assembly. In this section, we look at the advantages of using membrane adhesives in different applications.
- Automotive – In the automotive industry, membrane adhesive is used to bond and seal various components, including control panels, touch screens, and sensors, ensuring reliable performance in challenging conditions.
- Renewable Energy – In renewable energy systems, such as solar panels, membrane adhesive is used to protect and seal components exposed to outdoor conditions, ensuring long-term reliability.
- Electronics – In this industry, membrane adhesives are for protecting and sealing sensitive components, like flexible circuits and touchscreens. This adhesive is used to ensure high-quality display because of its optical clarity.
- Aerospace – Aerospace applications benefit from membrane adhesive’s ability to withstand extreme temperatures and vibrations while maintaining the structural integrity of critical components.
- Industrial Equipment – Membrane bonding adhesives impact industrial equipment’s durability by ensuring membrane components remain secure even in the harshest environments.
The versatility and reliability of membrane bonding adhesive make it an indispensable component in achieving robust assemblies, protecting sensitive components, and extending the lifespan of various products and systems across different industries.
Membrane Bonding Adhesives Compatibility with Various Membrane Materials
Here is what you need to know about adhesive compatibility with different membrane types.
- Rigid Substrates – In cases where membranes are bonded to rigid substrates, the adhesive should also be suitable for materials like glass, metals, or plastics, providing a reliable bond that withstands stress and environmental factors.
- Flexible Membranes – It is expected that this type of adhesive should be compatible with a host of materials, especially the ones used in membrane assembly. Compatibility ensures a strong and lasting bond without compromising the integrity of the membrane material.
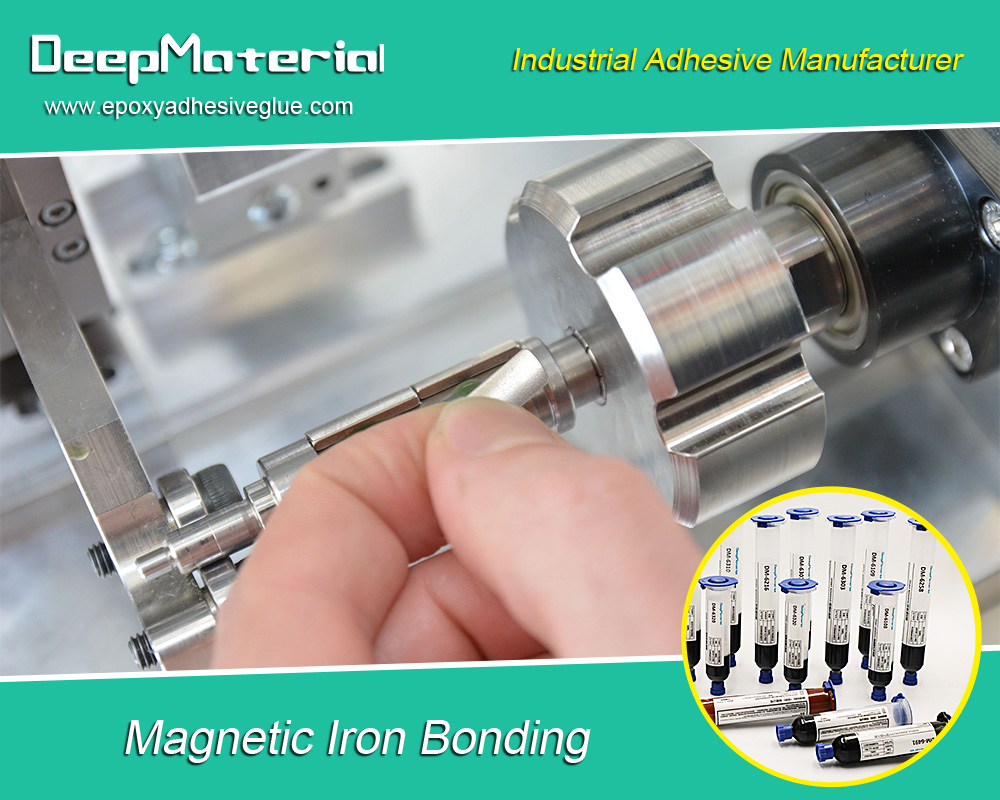
Final Words
Membrane bonding adhesives have proven to be the best option for securing membrane materials. In this post, we have looked at the benefits of using such adhesives in different industries. We have also considered the importance of material compatibility for the formation of long-lasting bonds. Precision bonding is equally important in dispensing membrane bonding adhesives.
For more about choosing the membrane bonding adhesive, you can pay a visit to DeepMaterial at https://www.epoxyadhesiveglue.com/category/epoxy-adhesives-glue/ for more info.