The Role of Pressure Sensitive Adhesive Manufacturers in the Packaging Industry
The Role of Pressure Sensitive Adhesive Manufacturers in the Packaging Industry
Pressure sensitive adhesives (PSAs) are ubiquitous in our daily lives. From the humble postage stamp to complex industrial packaging solutions, PSAs are everywhere, silently holding our world together. They are the unsung heroes of countless products that we use daily, ensuring that everything stays in place and reaches its destination safely and securely.
The manufacturing of these adhesives is a complex process that requires a deep understanding of chemistry, material science, and engineering principles. It’s a process that demands precision, consistency, and an unwavering commitment to quality. The manufacturers who undertake this task play a crucial role in the packaging industry, providing it with the tools it needs to protect and preserve a wide range of products.
In this blog post, we will delve deeper into the world of pressure sensitive adhesive manufacturers. We will explore their role in the packaging industry, examine their manufacturing processes, and discuss how they contribute to the industry’s ongoing evolution.
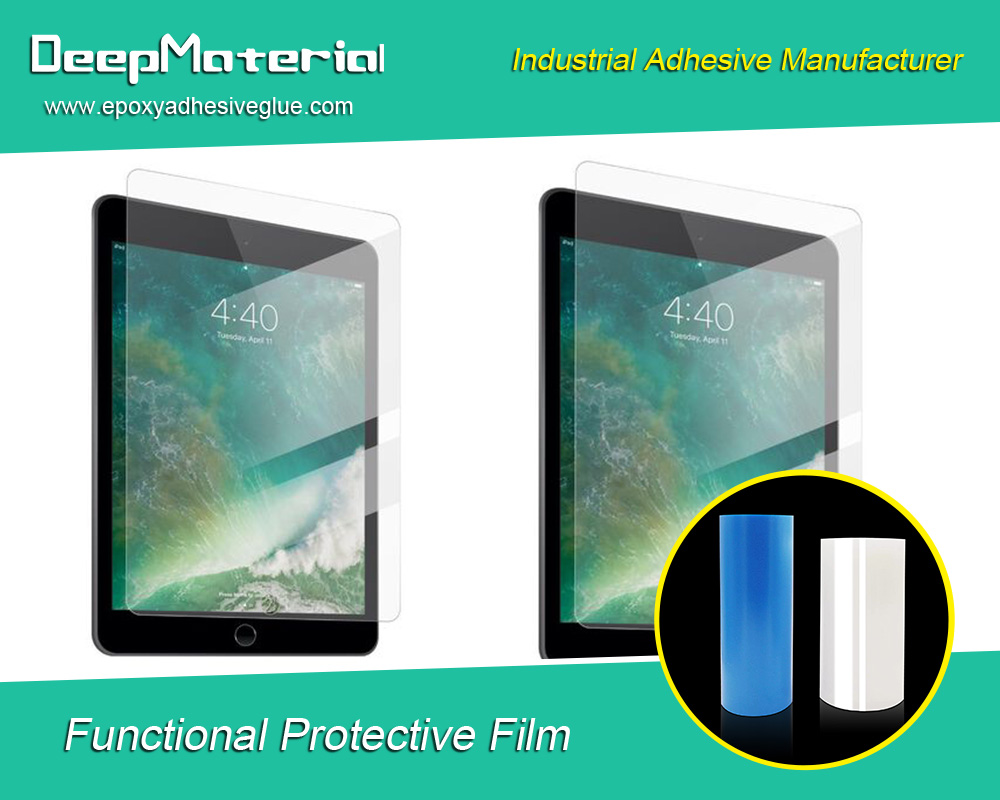
The Evolution of PSA Manufacturers in the Packaging Industry
Pressure sensitive adhesive has a long history in the packaging industry. It was first developed in the early 20th century and has since undergone significant advancements. Initially, PSA was made from natural rubber, but with the advent of synthetic materials, such as acrylics and silicones, the properties of PSA improved significantly. These synthetic materials offered better adhesion, durability, and resistance to temperature and moisture.
Over the years, PSA manufacturers have played a crucial role in the development and growth of the packaging industry. They have continuously improved their products to meet the changing needs of consumers and industries. The advancements in PSA technology have allowed for more efficient packaging processes, reduced waste, and increased product shelf life. Today, PSA manufacturers are at the forefront of innovation, constantly developing new adhesive solutions to address the evolving demands of the packaging industry.
The Key Players in the PSA Manufacturing Industry and their Market Share
The PSA manufacturing industry is highly competitive, with several key players dominating the market. Some of the major PSA manufacturers include 3M, Avery Dennison Corporation, Henkel AG & Co. KGaA, and Nitto Denko Corporation. These companies have a significant market share and are known for their high-quality adhesive products.
3M is one of the largest PSA manufacturers in the world, offering a wide range of adhesive solutions for various industries, including packaging. The company has a strong presence in the global market and is known for its innovative products and technologies. Avery Dennison Corporation is another major player in the PSA manufacturing industry, specializing in pressure-sensitive materials and adhesive solutions. The company has a diverse product portfolio and serves customers in industries such as packaging, automotive, and healthcare.
Henkel AG & Co. KGaA is a global leader in adhesive technologies, offering a wide range of PSA products for packaging applications. The company focuses on developing sustainable solutions and has made significant investments in research and development. Nitto Denko Corporation is a Japanese company that specializes in adhesive tapes and films. The company has a strong presence in the packaging industry and is known for its high-quality products.
The Advantages of Using PSA in Packaging and its Impact on the Industry
There are several advantages to using PSA in packaging. Firstly, PSA is cost-effective compared to other types of adhesives. It requires minimal equipment and labor to apply, reducing production costs. Additionally, PSA can be applied in various forms, such as tapes, labels, and films, making it versatile for different packaging needs.
PSA also offers excellent adhesion to a wide range of surfaces, including plastics, metals, and glass. This ensures that packages are securely sealed and protected during transportation and storage. Moreover, PSA provides a strong bond that is resistant to temperature changes, moisture, and other environmental factors. This helps to maintain the integrity of the package and extend the shelf life of the product.
The impact of PSA on the packaging industry has been significant. It has revolutionized packaging processes by providing a faster and more efficient way to seal packages. PSA eliminates the need for heat or solvent activation, reducing production time and energy consumption. It also reduces waste, as it can be easily removed and repositioned without damaging the packaging material. This not only saves costs but also contributes to a more sustainable packaging process.
The Different Types of PSA and their Applications in Packaging
There are several types of PSA available in the market, each with its own unique properties and applications in packaging. Some of the common types of PSA include acrylic, rubber-based, and silicone-based adhesives.
Acrylic adhesives are known for their excellent adhesion to a wide range of surfaces, including plastics, metals, and glass. They offer good UV resistance and temperature resistance, making them suitable for outdoor applications. Acrylic adhesives are commonly used in packaging tapes, labels, and films.
Rubber-based adhesives are known for their high initial tack and flexibility. They provide a strong bond to a variety of surfaces and are commonly used in packaging tapes and labels. Rubber-based adhesives are ideal for applications that require quick bonding and easy removal.
Silicone-based adhesives are known for their high temperature resistance and excellent release properties. They are commonly used in applications that require high heat resistance, such as automotive and electronics packaging. Silicone-based adhesives are also used in medical packaging, as they offer good biocompatibility and sterilization resistance.
The Role of PSA Manufacturers in Developing Sustainable Packaging Solutions
Sustainability is a growing concern in the packaging industry, and PSA manufacturers play a crucial role in developing eco-friendly packaging solutions. They are constantly working towards reducing the environmental impact of their products and processes.
PSA manufacturers are investing in research and development to develop adhesive solutions that are recyclable and biodegradable. They are also exploring alternative raw materials that are renewable and have a lower carbon footprint. Additionally, PSA manufacturers are collaborating with packaging companies to develop sustainable packaging designs that minimize waste and promote recycling.
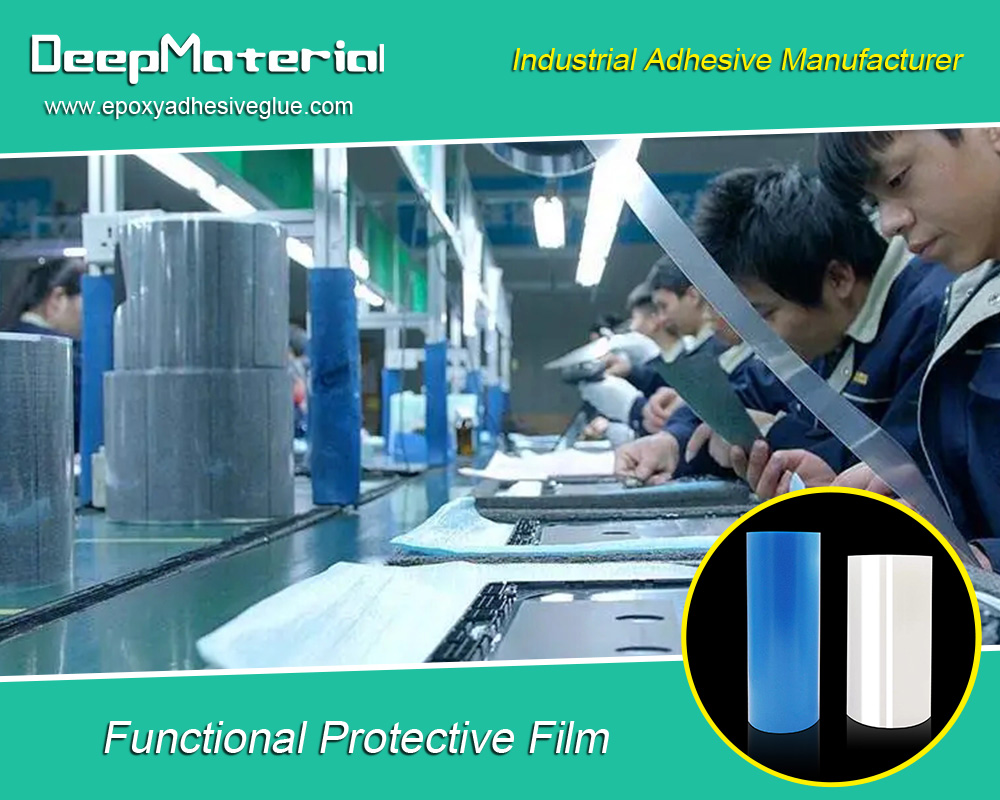
Conclusion: The Crucial Role of PSA Manufacturers in the Packaging Industry
In conclusion, PSA manufacturers play a crucial role in the packaging industry. Their adhesive solutions are essential for sealing and securing packages, ensuring product integrity during transportation and storage. PSA offers several advantages, including cost-effectiveness, versatility, and environmental benefits. PSA manufacturers are constantly innovating to meet the changing needs of consumers and industries, developing sustainable packaging solutions and advancing adhesive technology.
For more about choosing the Role of Pressure Sensitive Adhesive Manufacturers in the Packaging Industry, you can pay a visit to DeepMaterial at https://www.epoxyadhesiveglue.com/category/epoxy-adhesives-glue/ for more info.