What Are The Typical Application Methods Used By An Electronics Silicone Coating Manufacturer?
What Are The Typical Application Methods Used By An Electronics Silicone Coating Manufacturer?
Electronics silicone coating is an absolute must – without it, electronics are totally exposed to the elements and at serious risk of failure. Moisture can corrode delicate circuits, dust can clog up tiny parts and destroy performance, and temperature fluctuations could cause thermal stress that leads to the premature death of components.
But with a protective layer of silicone material safeguarding them from all those issues – you’re guaranteed optimal performance throughout their lifetime! It provides electric insulation as well as peace of mind, knowing they won’t be eaten away by Mother Nature anytime soon.
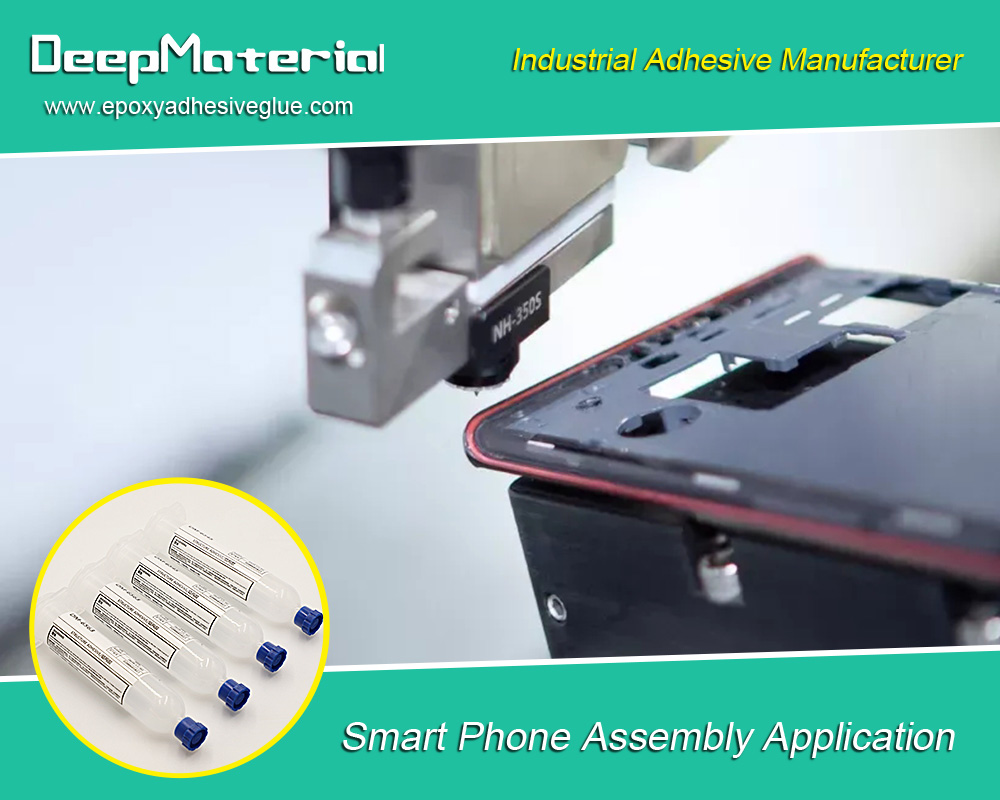
Importance of application methods in electronics silicone coating
The success of electronic silicone coating relies heavily on the method used for application. To make sure it’s applied in a uniform, even layer that sticks appropriately to all types of components, you need to use the proper technique. If not, there won’t be proper insulation or coverage – no matter how fancy the product.
If we take small and complex items as an example – they will need brushing, while more significant parts should be dipped or sprayed instead. It pays off to choose carefully which technique to use based on the size, shape, and complexity of components – otherwise, efficacy is lost quickly down the drain.
Brushing method
The brushing method of applying silicone onto electronic components is nothing short of a blessing! Finger snap precision and excellent reachability to the nooks and crannies — you get all that and more. Think circuit boards, connectors, sensors–this methodology literally gives you 360° control.
No wonder this technique has become so popular in recent years. But make no mistake: with every perk comes its drawbacks, too! It helps, sure, yet it requires quite a lot – of time (for intricate assemblies) as well as skill (to achieve uniform coating). Heck, even the brush itself can add extra particles or contaminants, resulting in performance issues down the road.
Dipping method
Plunging in is a great way to coat electronic parts – dip them into the silicone bath and pull them out for a smooth, even finish. Now, this process has its perks – it helps you save time and money by coating multiple pieces at once without wasting any material. Plus, every inch of your components will be nicely coated.
Still, there are some drawbacks worth considering. First up: disclaimer alert! You have to be careful when handling the parts because they could get damaged or contaminated. And if you want thick layers, you better prepare yourself; drying time can take forever – but don’t worry, it’ll be worth it in the end.
Spraying method
Spraying with a gun or nozzle to give electronic components just the right amount of silicone is one super quick way to get consistent coverage. Sure, it may be speedy, but there are certain downsides. You have to watch for overspray – which basically means you could waste buckets of material and risk polluting your surrounding environment.
Plus, if you don’t use proper ventilation techniques and safety measures, you’ll expose yourself and other people nearby to nasty inhaling particles from that fine mist. So sure – spraying can make life easier sometimes – but not without respecting the rules.
Flow coating method
The flow coating method gives you the option to completely cover components, regardless of their irregular shapes or complex geometries. It’s great in theory, but can it really provide reliable insulation and protection? Pour yourself a cup of coffee while I give you the details.
You’ll be happy to hear that this process can undoubtedly coat components ranging from small pebbles up to big rocks; basically, anything with a unique size or shape is covered! Plus, who wants thinner coverage when more robust protection is needed? Not only does the flow coating method dispense an even thicker layer of coating- like butter on toast -it’s not too obnoxious either! When appropriately applied, all access points get enough silicone material for overall coverage, and your surfaces remain neat and clean.
Vacuum impregnation method
The vacuum impregnation method is a luxurious procedure capturing precision where ordinary methods falter. It starts with placing the components into a chamber under a vacuum-like atmosphere, inducing traffic control as the silicone material glides into every corner of and around the hollowed objects in search of empty spaces to occupy, leaving no inch untouched.
A never-ending project that guarantees full coverage within shapes challenging even the most trained eye – making sure insulation reaches its summit peak with many air pockets filled along their safe paths for excellent protection down the road while also supplying plenty of options during acceleration since diverse levels of thickness are achievable throughout one batch alone!
Unfortunately, though, this vision doesn’t come easy or cheap. Specialized personnel and equipment are necessary, plus more time is added on top. At the same time, what usually takes seconds will exceed minutes and hours, respectively, from the preparation stage until cured correctly, ensuring all steps have been completed at an optimal level before given safety clearances can be granted.
Roll coating method
The roll coating technique offers a swift and efficient way of applying silicone solids to electronic components. This is especially true for lengthy or level parts, like flexible circuits or sheets. Not only does it enable high-volume manufacturing with minimal labor charges, but the precision and controllability of the thickness delivered are just right for when accuracy is paramount.
Still, such an approach has its drawbacks. Specialized machines used together with hefty set-up fees need to be taken into consideration. The roller rates pressure should be monitored attentively, too, in order to guarantee a smooth coat and spare delicate items from damage. Last but not least – due to the complexity factor – this methodology may not always work for complexly shaped devices with fragile surfaces.
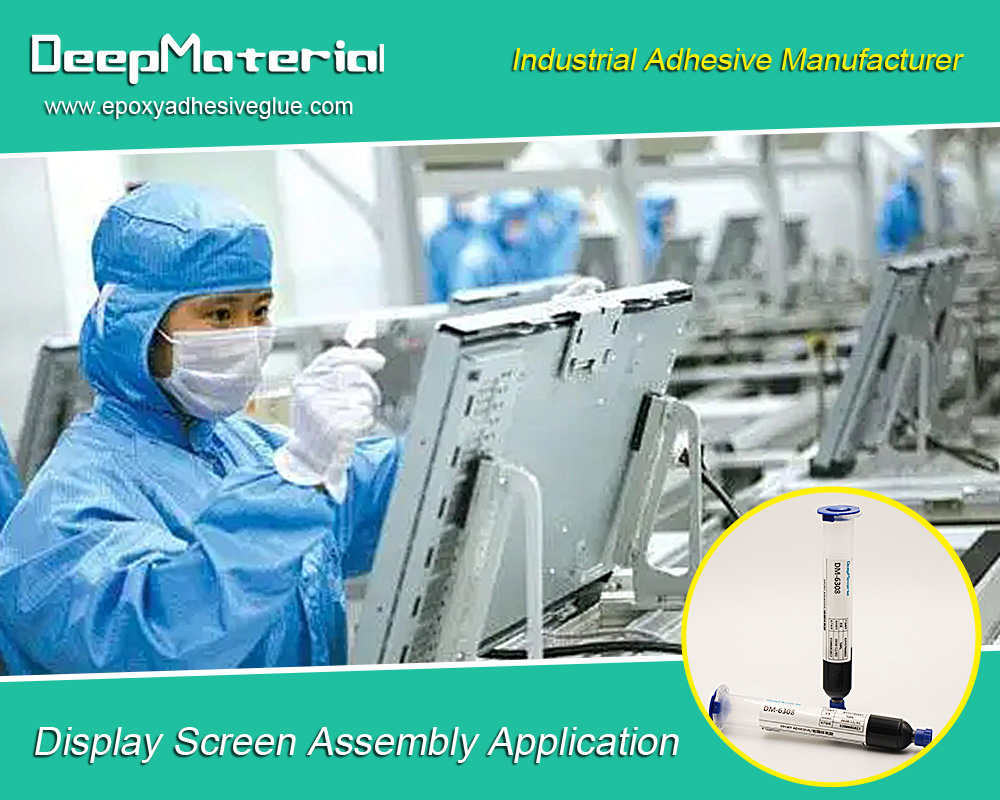
Conclusion
To wrap it up, electronic silicone coatings play an indispensable part in guarding tech components against all kinds of environmental conditions and guaranteeing their top performance plus durability. Picking the appropriate application method is critical to ensuring successful protection as well as insulation.
We have different application tactics, such as brushing, dipping, spraying, flow coating, vacuum impregnation, and even roll coating! Each one carries its benefits and shortcomings based on component size & shape, materials used, plus complexity.
For more about choosing the typical application methods used by an electronics silicone coating manufacturer, you can pay a visit to DeepMaterial at https://www.epoxyadhesiveglue.com/category/epoxy-adhesives-glue/ for more info.