What is the heat resistance and weatherability of automotive adhesives? Can they withstand the stresses in different environmental conditions?
What is the heat resistance and weatherability of automotive adhesives? Can they withstand the stresses in different environmental conditions?
Automotive adhesives are designed to withstand a wide range of environmental conditions and stresses encountered in automotive applications. Their heat resistance and weatherability can vary depending on the specific type of adhesive used. However, many automotive adhesives are formulated to exhibit excellent performance in demanding conditions.
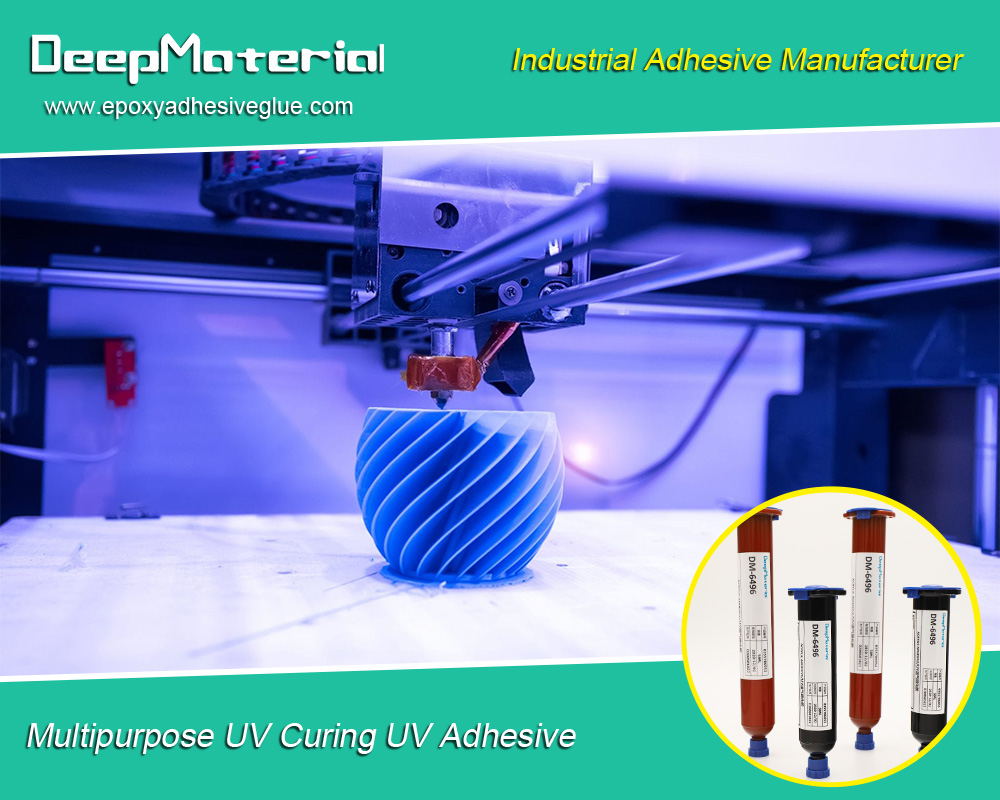
Here are some key points regarding the heat resistance and weatherability of automotive adhesives:
Heat Resistance
Automotive adhesives are often formulated to have high heat resistance to withstand the elevated temperatures encountered in engine compartments and other areas of a vehicle. They can typically withstand temperatures ranging from -40°C to 150°C or higher, depending on the adhesive type. Heat-resistant adhesives are often used in applications within the engine compartment, where temperatures can reach elevated levels.
Weatherability
Automotive adhesives are exposed to various weather conditions, including extreme temperatures, humidity, rain, snow, and UV radiation. These adhesives are formulated to resist degradation and maintain their performance under prolonged exposure to these environmental factors. They often incorporate additives such as UV stabilizers and antioxidants to enhance weatherability. UV resistance is particularly important as prolonged exposure to sunlight can cause adhesive degradation and reduced performance. This weatherability helps to prevent adhesive failure, degradation, or loss of performance over time.
Temperature Cycling
Automotive adhesives are tested for their ability to withstand thermal cycling, which involves repeated exposure to alternating high and low temperatures. This is important because vehicles undergo temperature variations during operation, and adhesives must be able to handle these cyclic stresses without losing their bond strength.
Chemical Resistance
Automotive adhesives are often engineered to resist various chemicals such as automotive fluids, fuels, oils, and cleaning agents. They are designed to maintain their integrity and adhesive properties when exposed to these substances, preventing degradation or failure of the adhesive bond.
Vibration and Impact Resistance
Automotive adhesives are also formulated to have good resistance to vibrations and impacts. They are expected to maintain their bond strength even when subjected to the mechanical stresses and vibrations experienced in a moving vehicle.
Environmental Stresses
Automotive adhesives are designed to withstand a range of environmental stresses, including thermal cycling, vibrations, mechanical loads, and chemical exposure. They need to maintain their bonding strength and flexibility under these conditions to provide durable and reliable bonding. Manufacturers perform extensive testing to ensure that their adhesives meet the required performance standards and can withstand the stresses encountered in automotive applications.
It’s important to note that the specific performance characterstics of an automotive adhesive can vary depending on the formulation, brand, and intended application. Manufacturers provide detailed technical specifications and guidelines for their adhesive products, which outline the recommended usage conditions and limitations. It’s advisable to consult the adhesive manufacturer or supplier for specific information on the heat resistance and weatherability of a particular automotive adhesive.
Automotive adhesives are formulated to withstand the stresses encountered in different environmental conditions. They are designed to provide strong and durable bonding under a variety of challenging situations. Here are some examples of the stresses that automotive adhesives can typically withstand:
Thermal Stresses
Automotive adhesives are engineered to withstand thermal cycling, which involves repeated heating and cooling cycles. These adhesives can accommodate the expansion and contraction of bonded materials as temperatures change, maintaining their bond integrity over a wide temperature range.
Vibrations and Mechanical Loads
Vehicles experience vibrations and mechanical loads during normal operation, including engine vibrations, road vibrations, and dynamic loads. Automotive adhesives are formulated to absorb and dampen these vibrations, reducing stress concentrations and preventing bond failure.
Chemical Exposure
Automotive adhesives may come into contact with various chemicals, such as fuels, oils, cleaning agents, and road salts. They are designed to resist chemical attack and maintain their adhesive properties in the presence of these substances.
Humidity and Moisture
Vehicles are exposed to high levels of humidity and moisture, especially in areas such as the underbody or interior compartments. Automotive adhesives are formulated to resist moisture penetration, preventing corrosion and maintaining their bonding performance in humid environments.
UV Radiation and Weathering
Automotive adhesives are exposed to sunlight and UV radiation, which can cause degradation and loss of adhesive properties over time. They are formulated with UV stabilizers and other additives to enhance their resistance to UV radiation and maintain their performance in outdoor applications.
It’s important to note that the performance of automotive adhesives can vary depending on the specific formulation, application method, and bonding substrates, also depend on other factors, such as surface preparation, application method, and the specific bonding substrates. Manufacturers of automotive adhesives usually provide detailed technical specifications and guidelines regarding the heat resistance and weatherability of their products, which can help users select the appropriate adhesive for specific applications and environmental requirements, and ensure its suitability for a particular application and environmental conditions.
Conclusion
Automotive adhesives are designed to withstand various environmental conditions and stresses in automotive applications. Their heat resistance and weatherability can vary depending on the specific adhesive type used. Key points include heat resistance, which can withstand elevated temperatures in engine compartments, weatherability, which can be -40°C to 150°C or higher, chemical resistance, vibration and impact resistance, and environmental stresses.
Heat resistance is crucial for automotive adhesives to withstand extreme temperatures, humidity, rain, snow, and UV radiation. They are formulated to resist degradation and maintain performance under prolonged exposure to these factors. Thermal cycling, chemical resistance, and vibration and impact resistance are essential for adhesion.
Environmental stresses, such as thermal cycling, vibrations, mechanical loads, and chemical exposure, require adhesives to maintain bonding strength and flexibility. Manufacturers provide detailed technical specifications and guidelines for their adhesive products, ensuring they meet performance standards and can withstand the stresses encountered in automotive applications. Consult the adhesive manufacturer or supplier for specific information on the heat resistance and weatherability of a particular adhesive.
The performance of automotive adhesives can vary depending on the specific formulation, application method, and bonding substrates. Manufacturers typically provide detailed technical specifications and guidelines to help users select the appropriate adhesive for specific applications and environmental requirements.
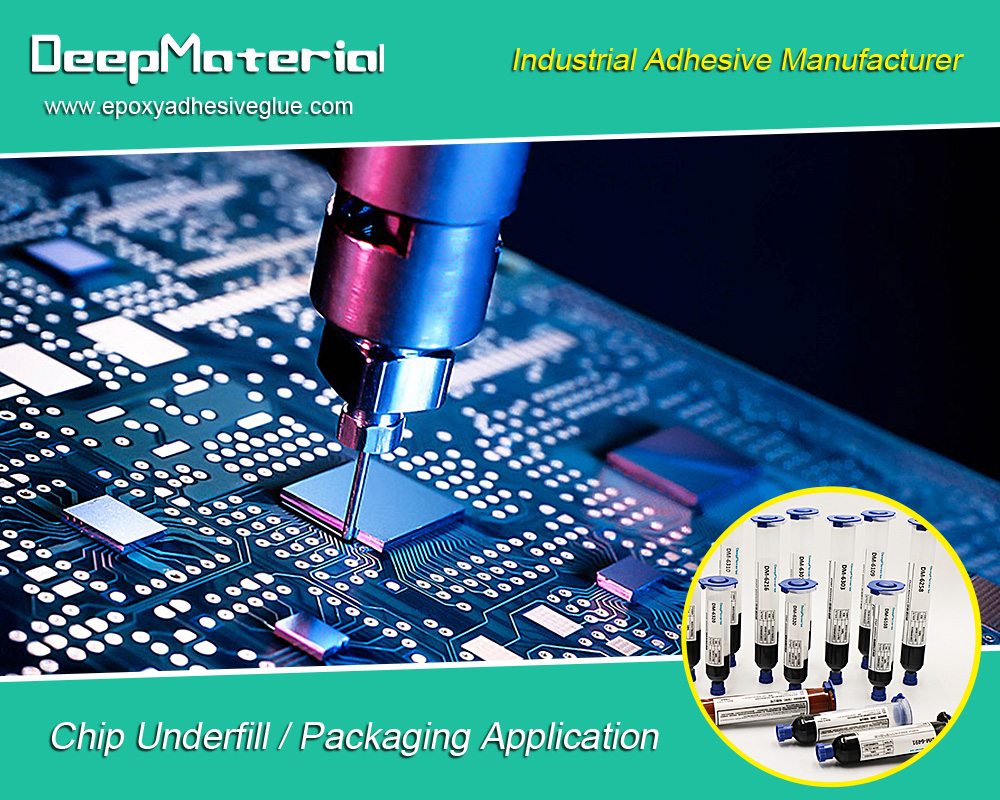
For more about choosing the best automotive adhesive,you can pay a visit to DeepMaterial at https://www.epoxyadhesiveglue.com/category/epoxy-adhesives-glue/ for more info.